From Manual Trolley to RGV or AGV
Jendamark’s production transport systems provide a modern, flexible and scalable alternative to traditional conveyor systems.
Built around a no-frills industrial trolley, our core unit is easily customised.
Simply add a bolt-on module to create either an RGV for precise movement along fixed rails, or an AGV for free-ranging navigation within your facility.
The choice is yours.
Our transportation platform allows you to choose a manual trolley, rail-guided vehicle (RGV) or automated guided vehicle (AGV).
Upgrade or scale as needed – with minimal downtime.
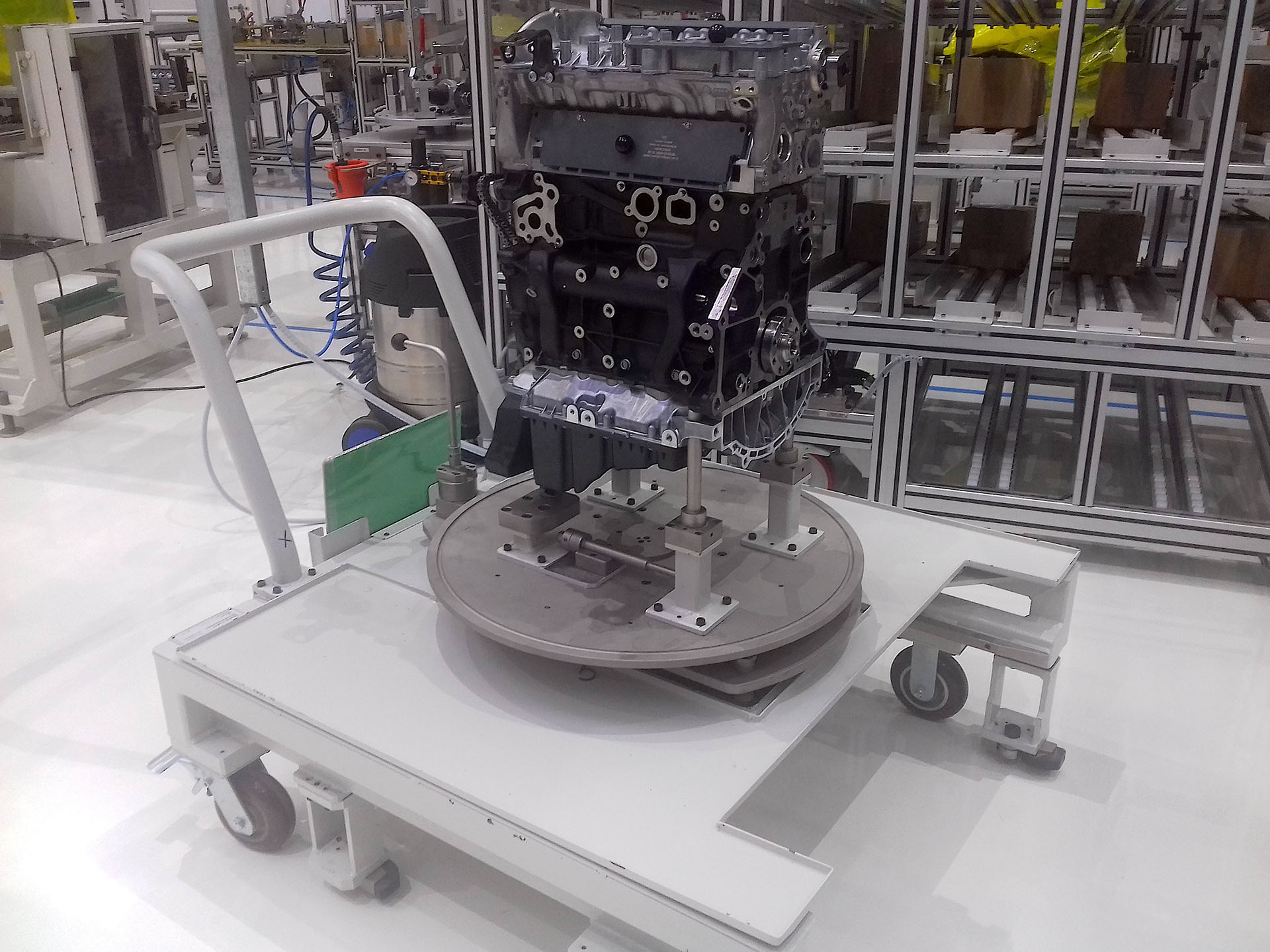
Manual Trolley
Manual trolleys represent a relatively low upfront investment, making them a cost-effective solution for basic material transport, which can be adapted to carry a variety of part sizes and shapes.
These trolleys are built to withstand the rigours of heavy industrial use in harsh factory environments.
Minimal operator training is required, allowing for immediate deployment. Operators have full manual control over the movement and handling of materials.
Guided Vehicle Specifications
Speed: 900mm/s
Acceleration: 4/-00mm/s2
Payload: 1000 kg
Parking precision: X +10mm/2mm and Y 10mm/2mm
Steering system: Differential/Rail
Drive system: Traction motor/s
Orientation/Navigation system: Camera line following/2D matrix/Rail
Debris clearance: Yes
Charging system: Contact pads
Energy storage system: Li-ion
Control and communication: Siemens
Interface to production line: Wi-Fi
Safety system: SICK
Certification: CE
Rail Guided Vehicle (RGV)
RGVs operate on a fixed rail guidance system, moving at a predictable speed along a dedicated path. This ensures accurate and repeatable movements, suited to applications demanding precise positioning and alignment.
Stability: RGVs can handle heavy loads, making them ideal for transporting large, bulky materials on production lines.
Efficiency: The rail-guided system enables RGVs to perform certain operations directly (unlike AGVs, which transfer to buffer stations). Because RGVs move predictably along a fixed path, they can optimise material flow in high-volume operations, while allowing operators to move freely around the workpiece.
Consistency: Properly installed rail systems offer a durable and reliable material transport method.
Automated Guided Vehicle (AGV)
AGVs excel in dynamic environments, adapting to changing layouts and obstacles. Where RGVs are constrained to rail systems, AGVs use optical navigation and are able to move more freely with flexible routing.
Flexibility: AGVs can be rerouted with ease.
Adaptability: AGVs can be adapted for a variety of tasks and changing workflows.
Scalability: AGV systems are highly scalable, allowing businesses to add or remove as production demands fluctuate.
Safety: Advanced sensor technology and navigation systems detect obstacles and avoid collisions.
Accessibility: AGVs are designed with ergonomics in mind, allowing the operator to work right around the vehicle.
Reduced infrastructure investment: Because AGVs don’t require fixed systems, installation costs are reduced, and disruptions to existing operations minimised.
Jendamark’s production transport solution can be customised according to customer requirements, including safety features, battery life or attachments for different materials, as well as charging options and docking mechanisms.
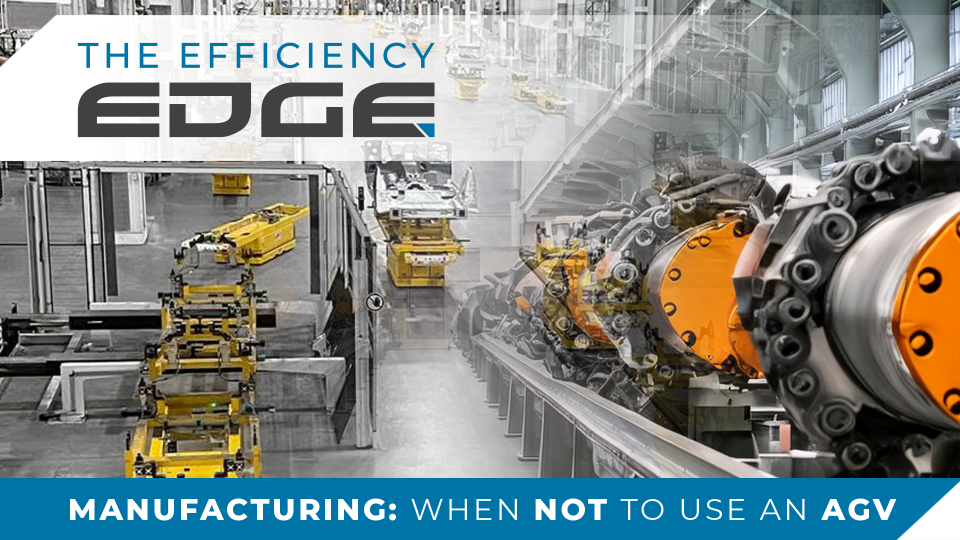
Manufacturing: When NOT to use an AGV
Read about the practical considerations that could impact your decision on whether or not to implement a transport system in your facility.