Exhaust systems
Catalytic Converter Assembly
From automated canning lines to modular, end-of-line assembly systems, Jendamark has developed a range of flexible solutions to help customers keep pace with changing emissions standards and product requirements.
Canning Lines
Adaptive canning has become a watchword in the automotive industry as OEMs require increasingly complex catalytic converters to comply with the emission control regulations in different markets. Jendamark’s standard canning machines can be configured in a variety of ways to meet process requirements and offer maximum flexibility and scalability when it comes to adding product variants and fluctuating volumes.
Jendamark’s canning solutions are proven in industry and are suitable for both passenger and commercial vehicles.
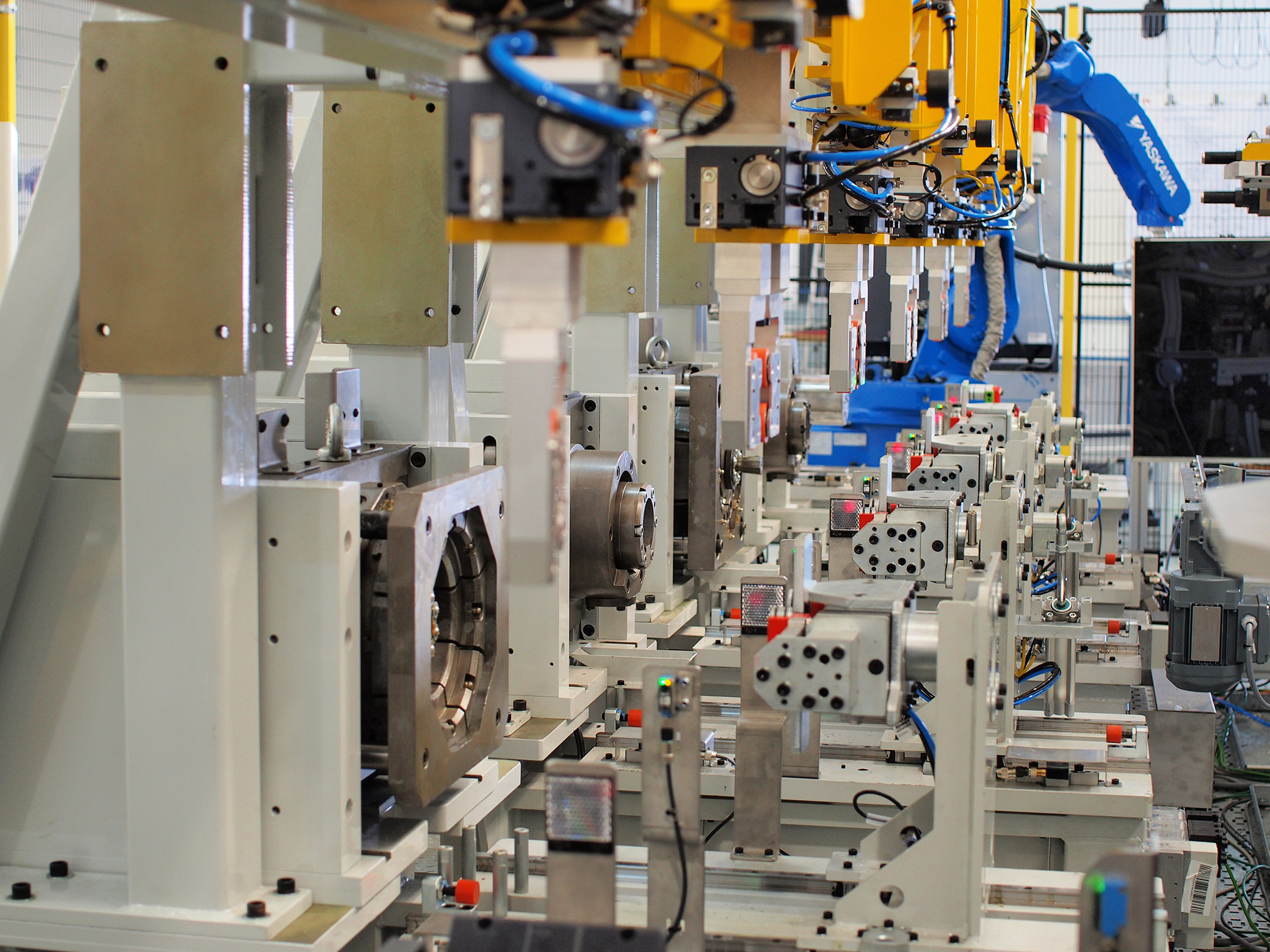
Standard canning modules
Our standard canning modules are easily configured to create a customised canning line solution that meets the customer’s exact specifications. Our standardised machines can easily be arranged to form manual, semi-automated or fully automated canning lines. Whether the process is GBD or non-GBD controlled, post-sizing (soft stuff) or pre-sizing (hard stuff), Jendamark has a solution.
Our Standardised Machines
Auto Stuffing Press
Mat Weighing and Sorting | Wrapping and Stuffing
- Servo mat sorting and transfer facility with 2 or 4 mat cartridges
- Mat scale with transfer to wrapper
- 3-5 position mat buffer
- Offline auto wrapper with transfer to press
- Servo stuffing press
- Auto can rotation (option)
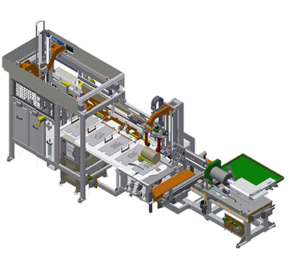

Measuring Machine
Mono Measuring | GBD Measuring
Manual
- High speed laser, mounted on servo vertical axis
- Servo turntable
- Beckhoff Industrial PC with Labview application
- Gigabit ethernet camera to read and determine position of mono face code
- Best fit GBD and local gap measurement
- Label printer
Automatic
- Simplified design
- High speed laser, mounted on servo vertical axis
- Servo turntable
- Gigabit ethernet camera to read and determine position of mono face code (optional)
- Beckhoff Industrial PC with Labview application
- Best fit GBD measurement and local gap (optional)
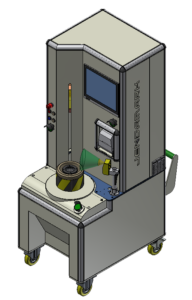
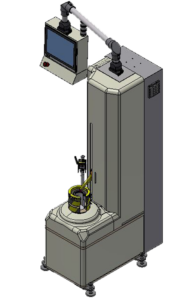
Can Orientation Machine
Can Orientation
- Can orientation on weld seam or can feature
- Sensor chosen based on required orientation feature on can
- Servo driven turntable
- Lighting can be added if required
- Part in place sensing
- Pneumatic 3-axis pick and place system to fetch cans from conveyor and place parts on orientation table

Forming Machine
Can Expansion | End Forming
- Servo roller/ball screw actuation
- Part handling with/without part rotation or robot handling
- Machine types include end form up, end form down, expansion, hole piercing
- Double shrinking machine also available
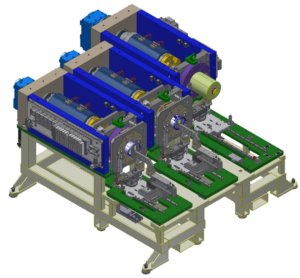
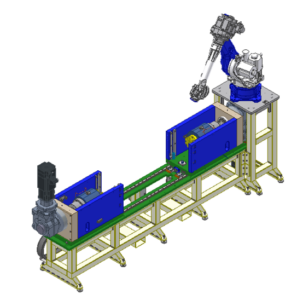
Shrinking Machine
Part Shrinking
Passenger Vehicle
- 12 tool segments
- Servo roller screw drive mechanism
- 12mm radial jaw movement
- Part loading and auto-eject facility
- Linear motor and pneumatic arms to transfer part in and out of machine drum
- Guarding and light curtains for use in manual lines
Commercial Vehicle
- 16 tool segments
- Servo roller screw drive mechanism
- 12mm radial jaw movement
- Part loading and auto-eject facility
- Servo-controlled positioning inside the machine
- 46-second auto tool change mechanism
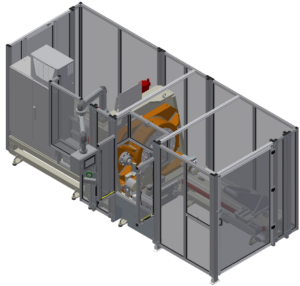
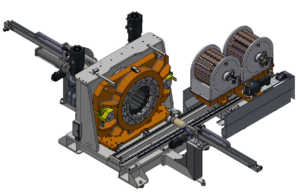
Marking Machine
Marking
Passenger Vehicle (Option 1)
- Pin marker on servo axis to cater for different part diameters
- Fixed scanner for DMC verification (option to put this on stepper axis)
- Pneumatic door with safety bump stop
- Automatic weld seam detection
Passenger Vehicle (Option 2)
- Two-pin marking machine (laser marking optional)
- Push-out test machine
- Servo press ram
- Force monitoring
- Displacement monitoring
- DMC verification scanner
- Two servo rack and pinion transfer units
- Reject chute (with lockable cover)
- Good parts chute
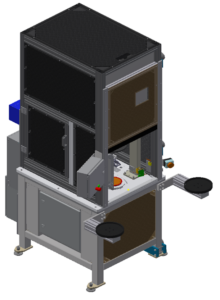
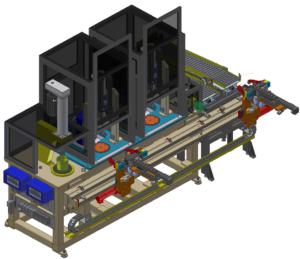
Commercial Vehicle
- Laser or pin marking options
- GBD measuring machine
- DMC verification scanner
- Two servo rack and pinion transfer units
- Reject chute (with lockable cover)
- Good parts chute
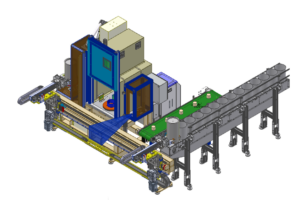
Our Different Processes
Non-Adaptive Stuffing
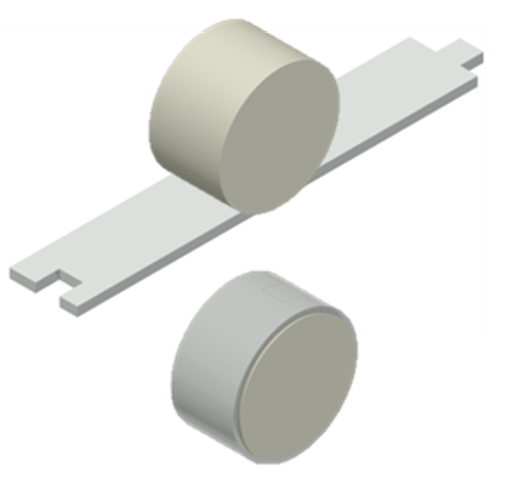
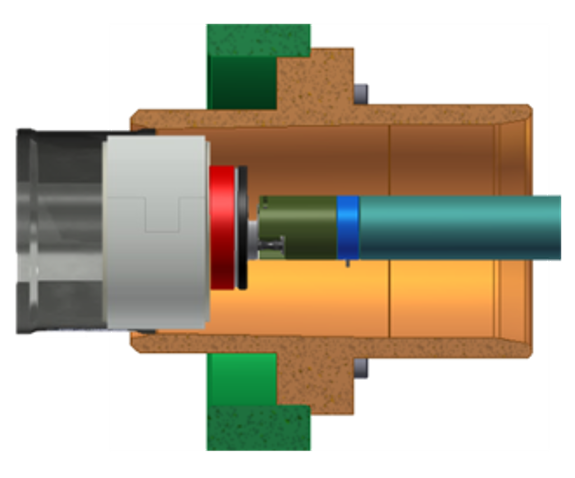
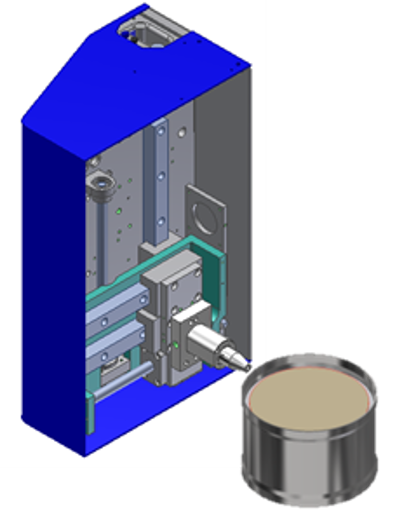
Non-GBD Pre-Sizing
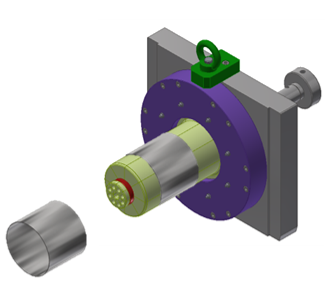
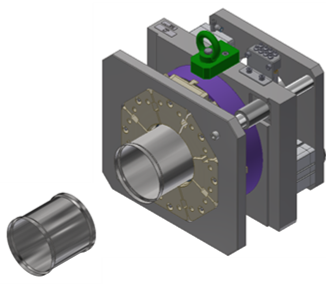
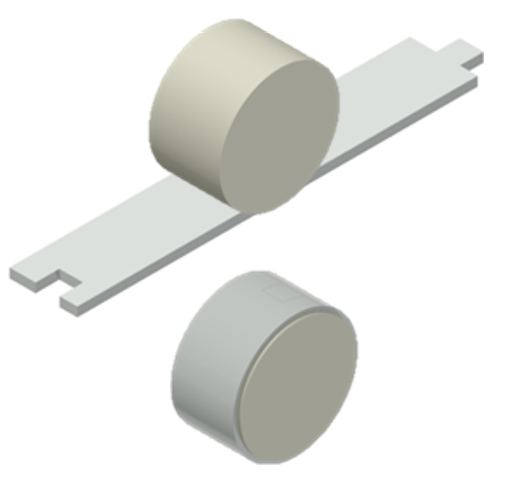
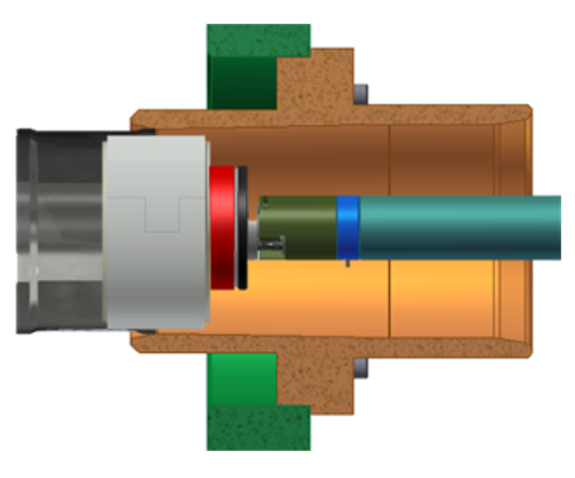
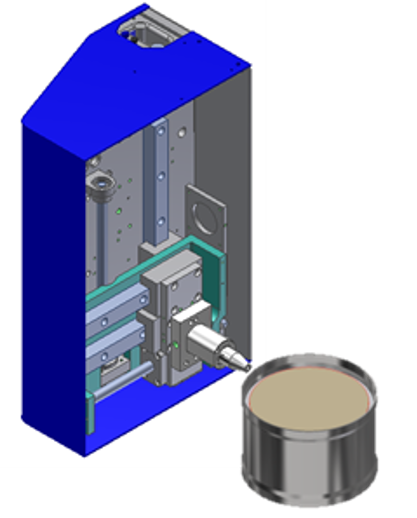
Non-GBD Post-Sizing
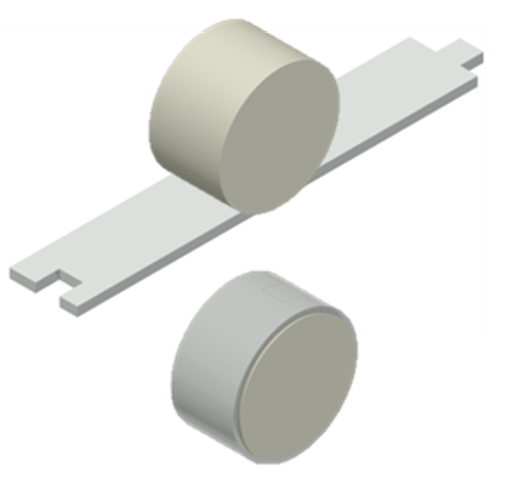
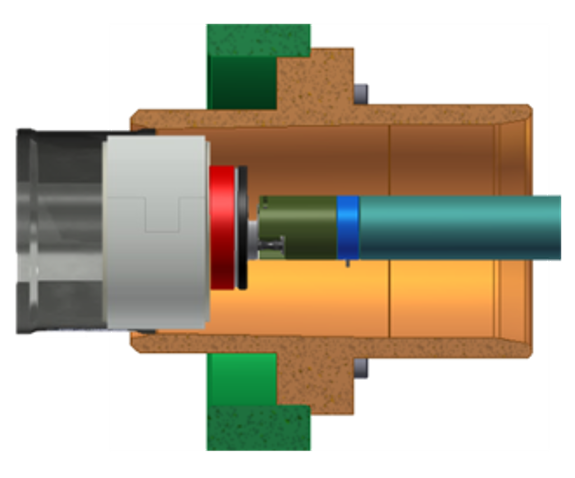
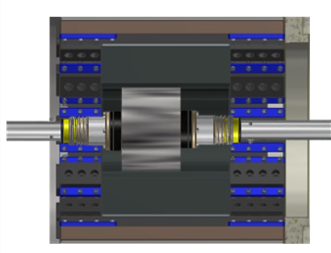
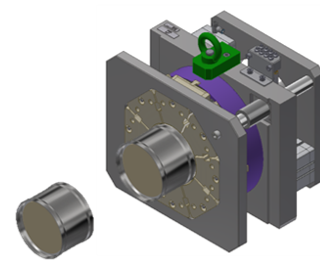
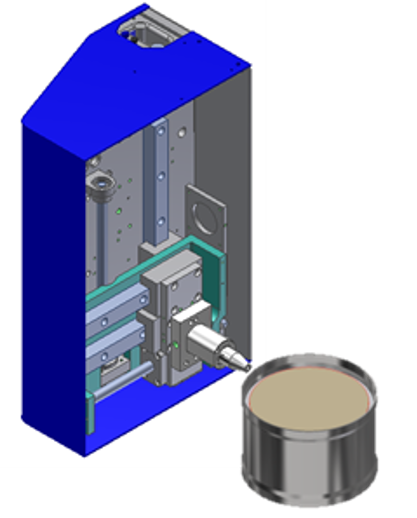
GBD Pre-Sizing
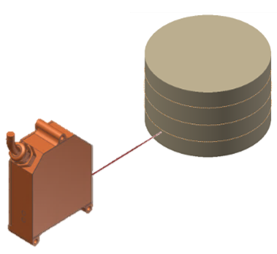
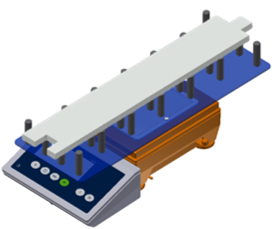
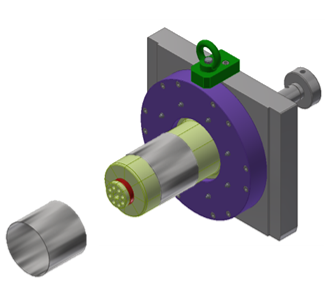
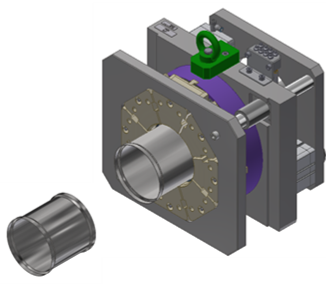
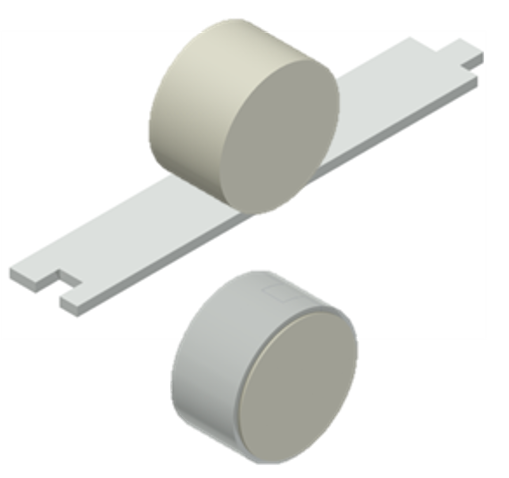
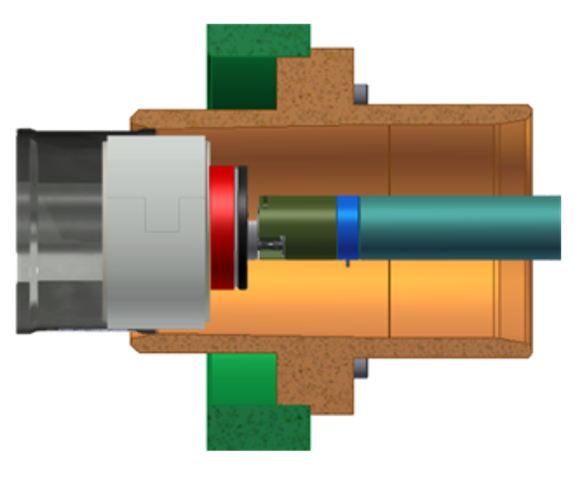
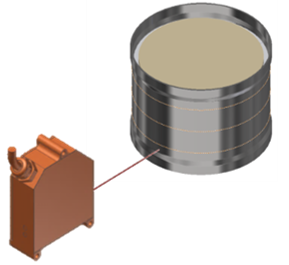
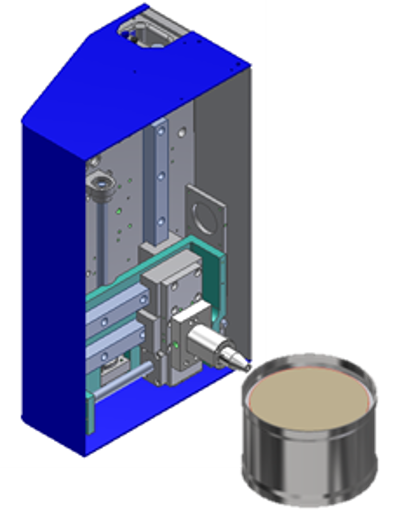
GBD Post-Sizing
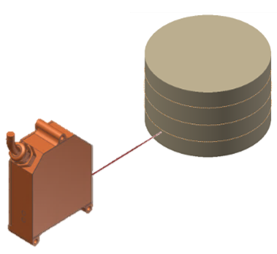
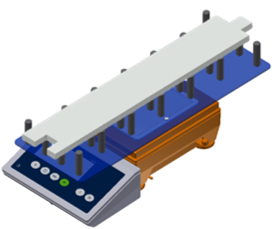
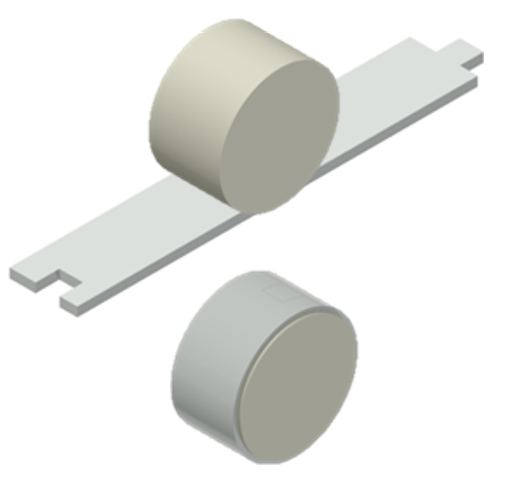
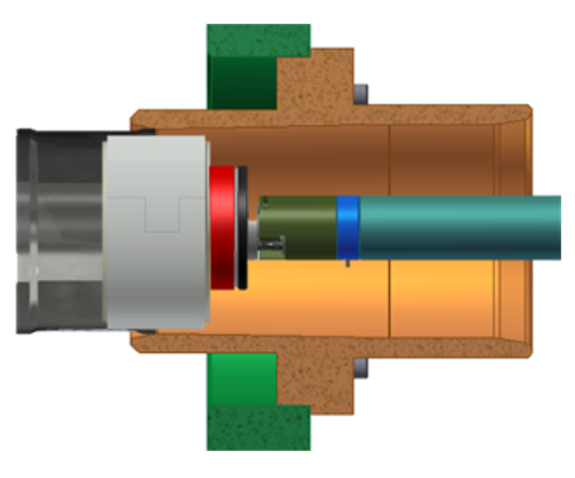
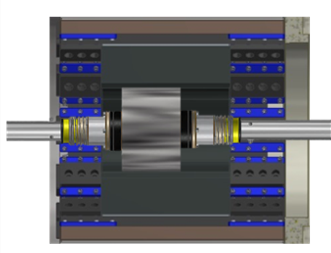
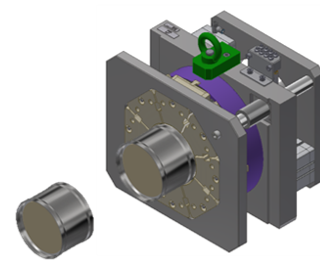
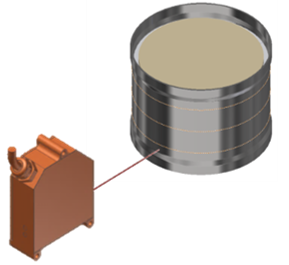
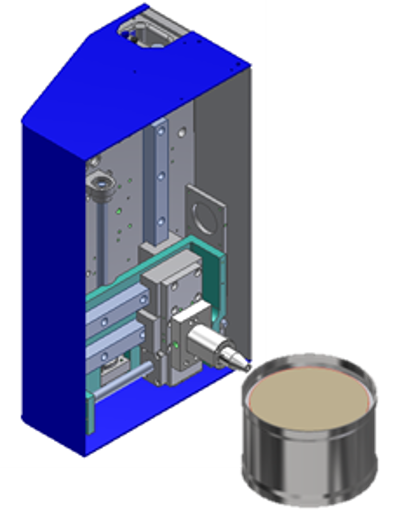
Catalytic Converter Assembly Lines
Jendamark also offers end-of-line catalytic converter assembly systems where the products that come off the canning lines are combined with other elements into a bigger assembly, ready for installation into the vehicle.
Assembly includes rigorous testing, marking, gauging and checking to ensure that the finished product meets the highest quality standards.
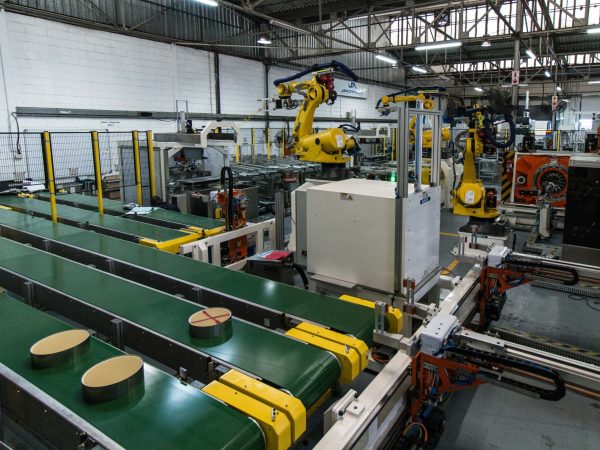
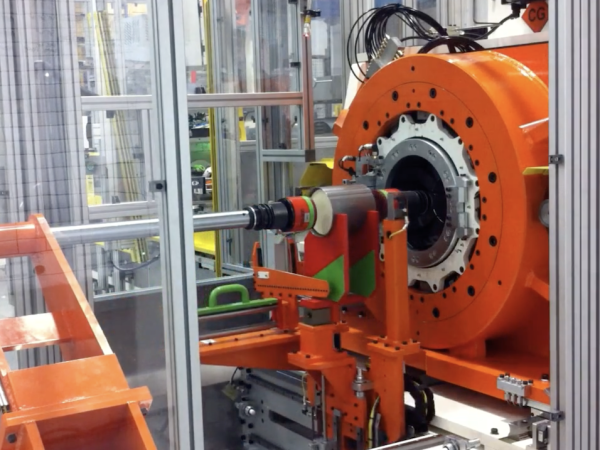
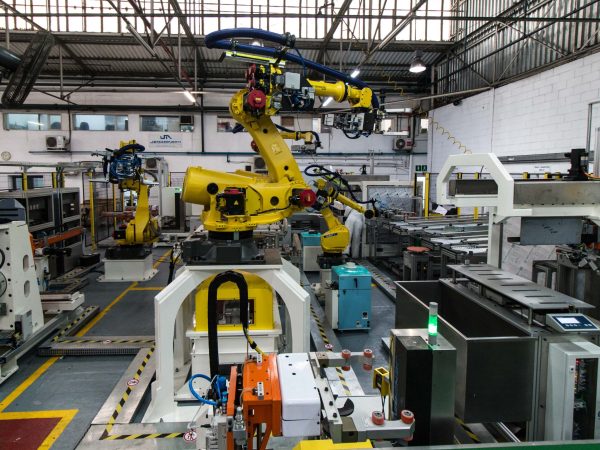
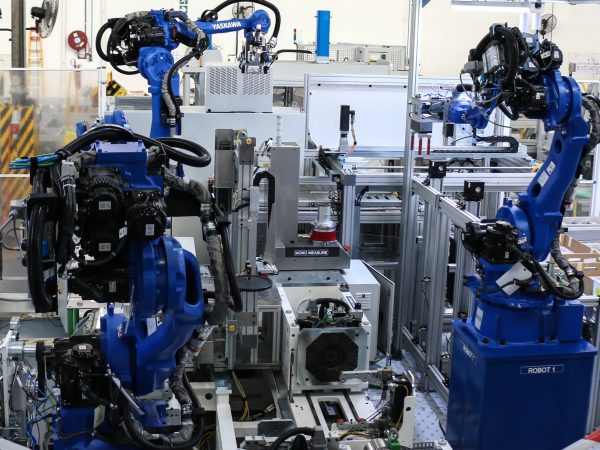
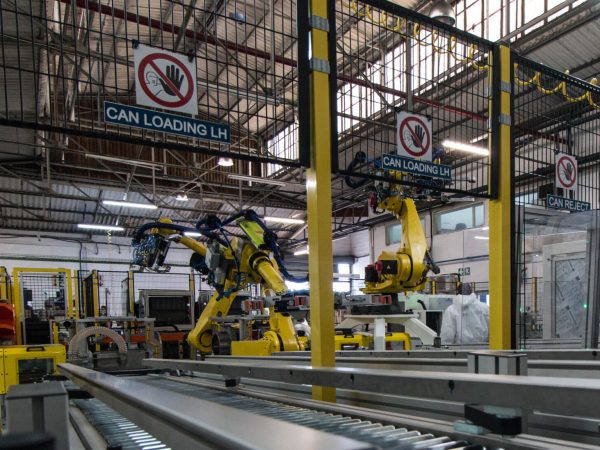
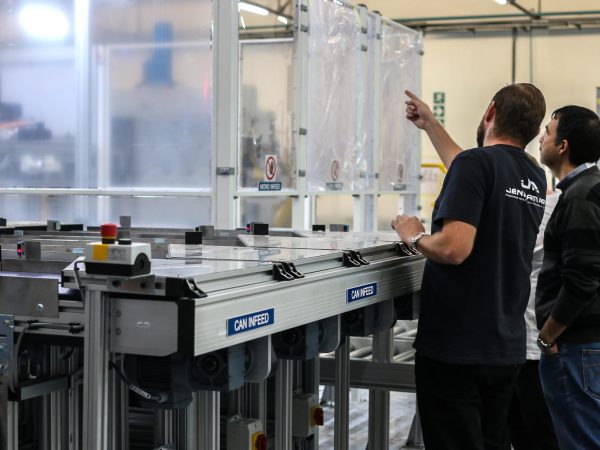
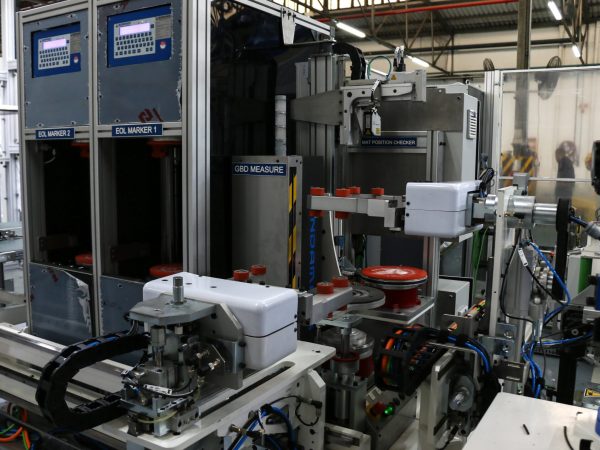
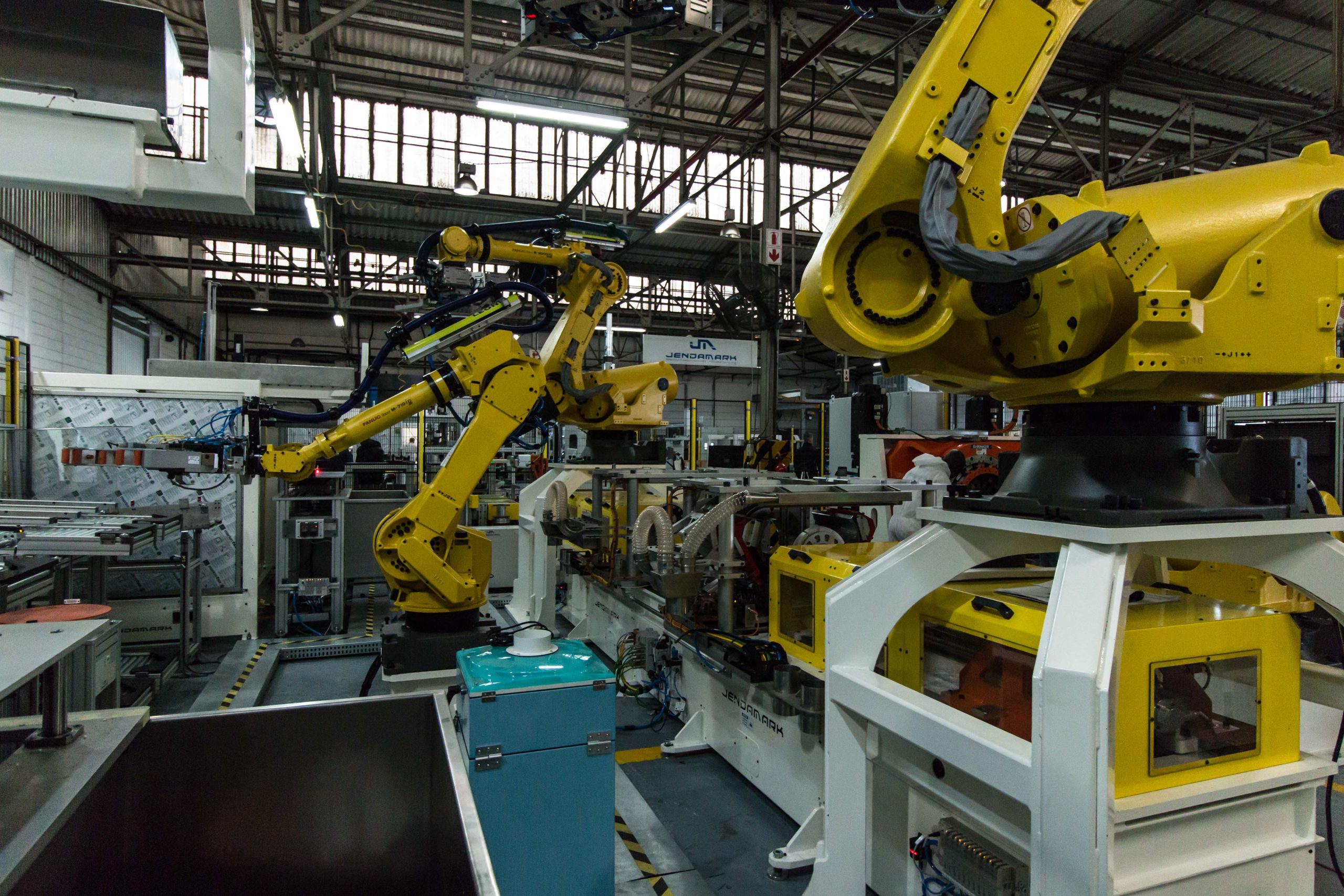
Save with building block production lines
Our canning lines are built using a building block approach – saving you both time and money.