- Case Study
- LIVGUARD
Laser Welding Machine
Ensuring safe and accurate EV battery module assembly
How our automated laser welding machine gave Livguard a safer, flexible solution for EV battery module assembly
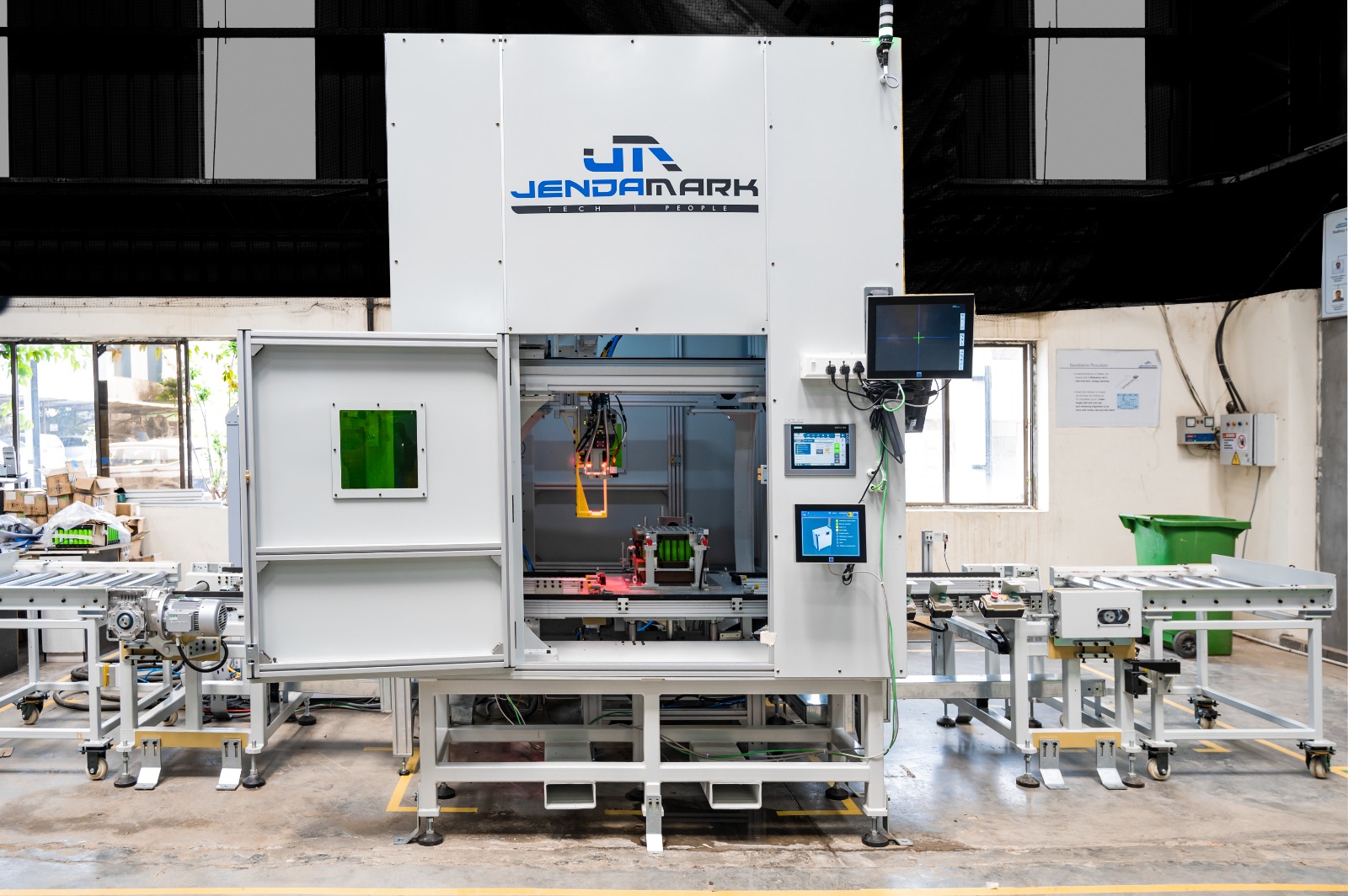
Customer Requirements
The customer approached Jendamark for a safe, automated laser welding solution for their EV battery module assembly that could:
- Eliminate human involvement in the welding process
- Safely and consistently weld busbars onto battery modules
- Accommodate various module shapes, sizes, and busbar arrangements using poka-yoke principles for error-proofing.
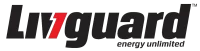
About the Customer
Livguard, a brand under the SAR Group, is a leading provider of energy storage solutions. Their offerings span inverters, automotive and solar batteries, stabilisers, and electronics manufacturing services.
- JENDAMARK DELIVERED
- Gurgaon, India
Key Challenges
- Different module shapes and sizes:
Each of the battery module variants has a different shape and size according to the number and arrangement of cells, with each module first formed before the busbar is placed on it.
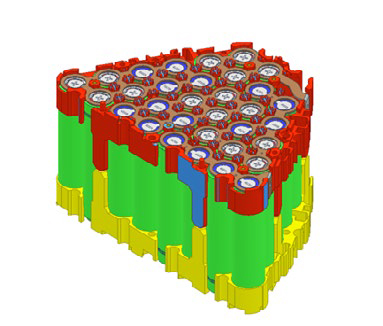
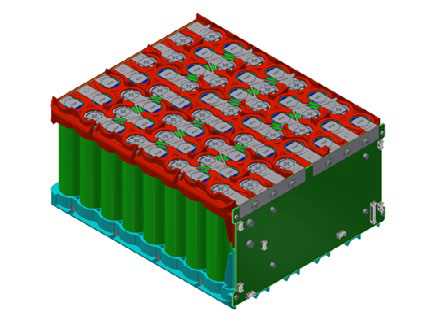
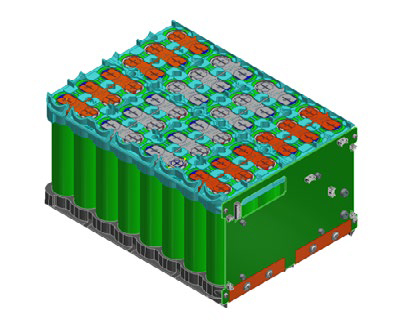
- Varying busbar arrangement and placement:
Aside from the different shapes and sizes of the modules, the busbar placement in the cell holder also differs according to the particular poka-yoke (foolproofing) arrangement.
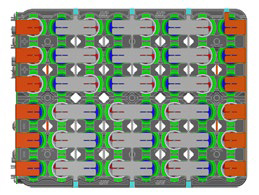
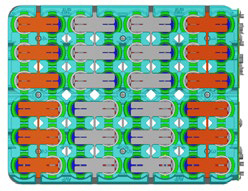
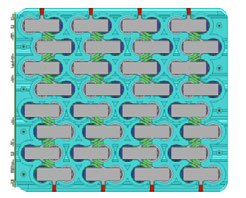
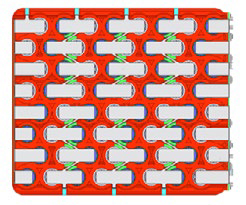
Our Solution
Solution 1 – Automatic laser welding machine:
Programmed and sequenced to carry out laser welding without any human intervention.
Solution 2 – Custom jigs and fixtures:
These were designed according to each module size and geometry to ensure uniform busbar height for welding. Fixtures were built to compensate for stack-up tolerances of the cell, cell holder and busbar, to ensure positive terminal-to-busbar contact during welding.
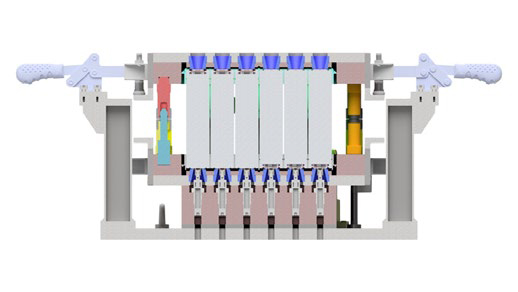
Solution 3 – Universal pallet:
Our conveyor-based pallet design accommodates various fixtures for different module types.
Solution 4 – Online busbar height verification:
Using a distance sensor to verify the busbar height before starting to weld ensures optimal focal length during welding.
Solution 5 – Dynamic laser head:
This powerful laser is capable of welding two different materials ranging from 0.2 mm to 2 mm in thickness.
Solution 6 – Recommended design modification:
To achieve accurate placement of busbar, we suggested minor product changes – protrusions on the module and corresponding holes in the busbar.
Customer Benefits
Standalone, flexible machine:
Independent of the main assembly line, the machine can be placed anywhere on the shop floor.
Future-ready design:
A universal pallet and adaptable programming allow quick integration of new variants using machine learning.
Vision-guided precision welding:
The built-in vision system detects the position of the tool and compensates for position error, if any, to achieve accurate laser welding.
Conclusion
Transforming a complex requirement into a reliable, automated process, Jendamark delivered a flexible, vision-enhanced laser welding solution. This not only met Livguard’s immediate needs but also set the stage for future scalability and modularity in EV battery assembly. The integration of IoT and machine learning proved key to unlocking a robust, intelligent manufacturing solution.