- Case Study
- ZF WORLDWIDE
Differential Assembly Lines
Make it modular:
Standardising diff assembly
How our building block lines provided a standardised, flexible solution for ZF facilities worldwide.
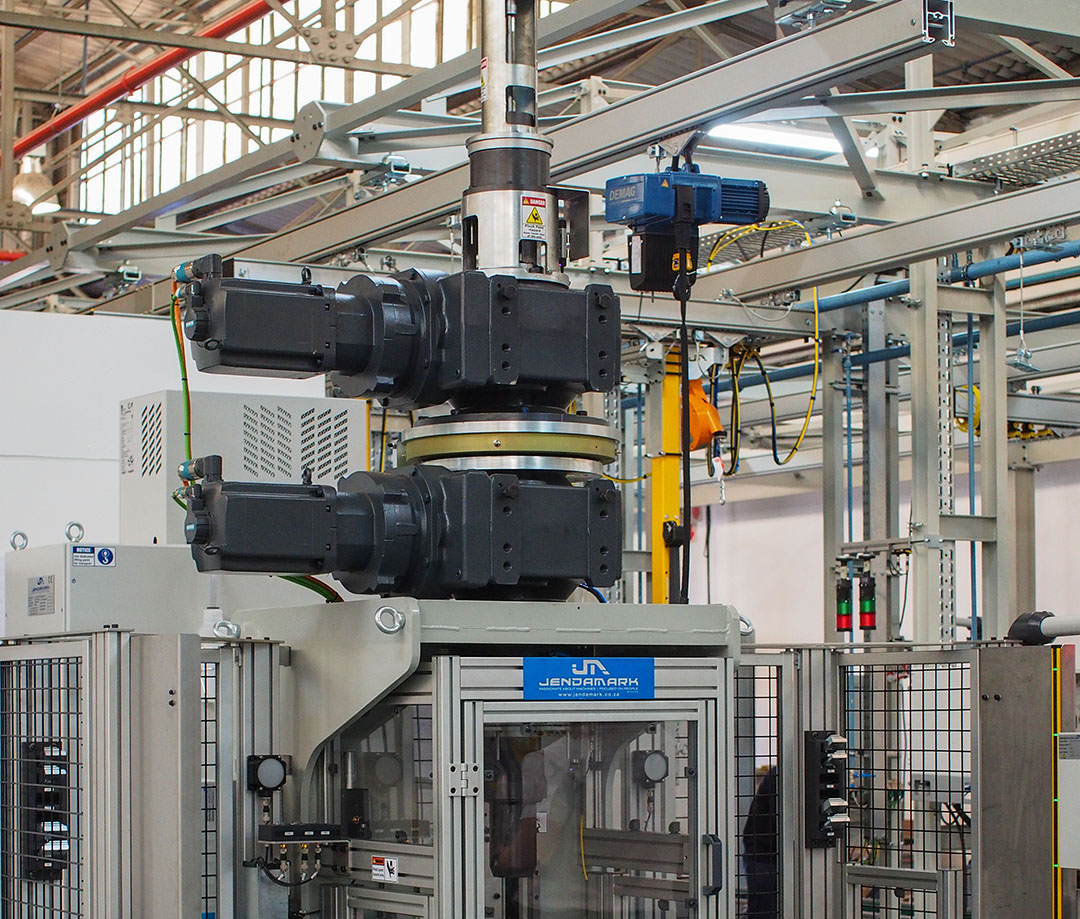
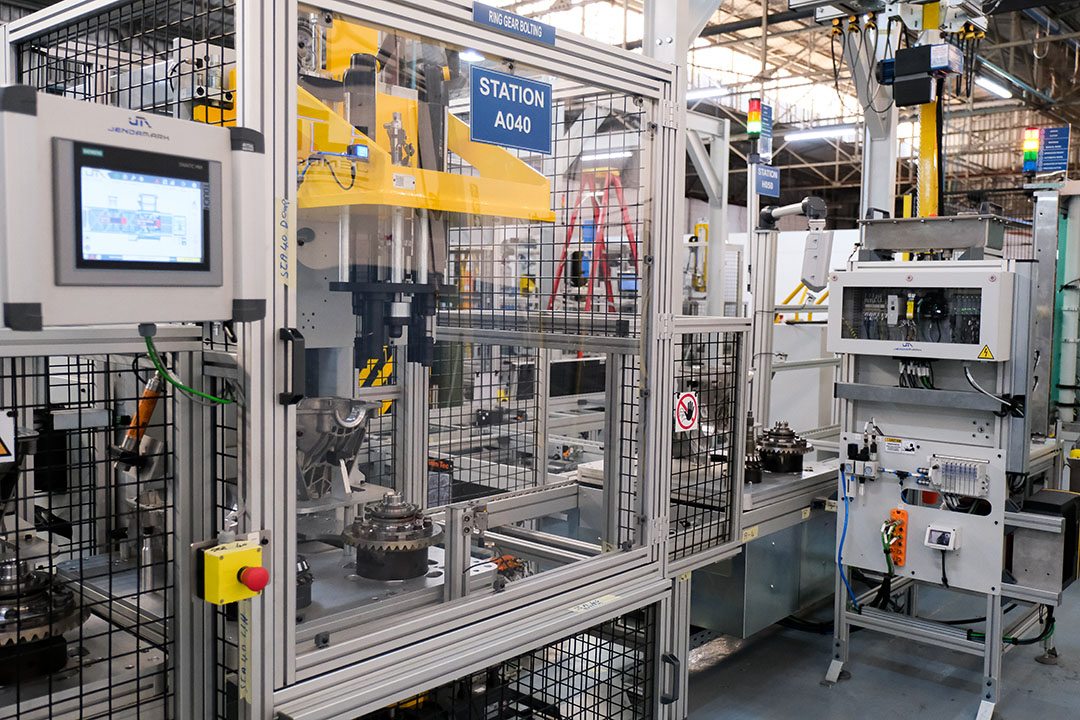
- JENDAMARK DELIVERED
- Worldwide
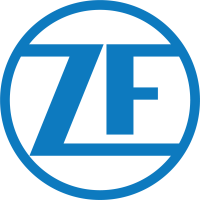
About the Customer
ZF is a global technology company that specialises in mobility solutions for various sectors, including automotive and industrial technology. They develop and produce advanced mobility products and systems, with a focus on reducing emissions and enhancing safety. Mobility solutions include transmissions, axles, and other driveline components for passenger cars and commercial vehicles.
Key Challenges
The customer needed a standardised yet flexible differential assembly solution for their facilities worldwide.
Most differential assembly lines have a common objective – to take a number of measurements in order to select and insert the correct set of shims that ultimately ensure the correct meshing of the differential gears. As a result, there are shared critical processes, such as the gauging and measurement of backlash and torque to turn, and certain critical machines that carry these out.
Every machine builder has their own ways of executing their critical machines from a mechanical and software perspective, which has an effect on the assembly process.
For example, which transducer the builder chooses for a machine has an impact on everything from the consistency and commonality of backlash measurement to shim selection.
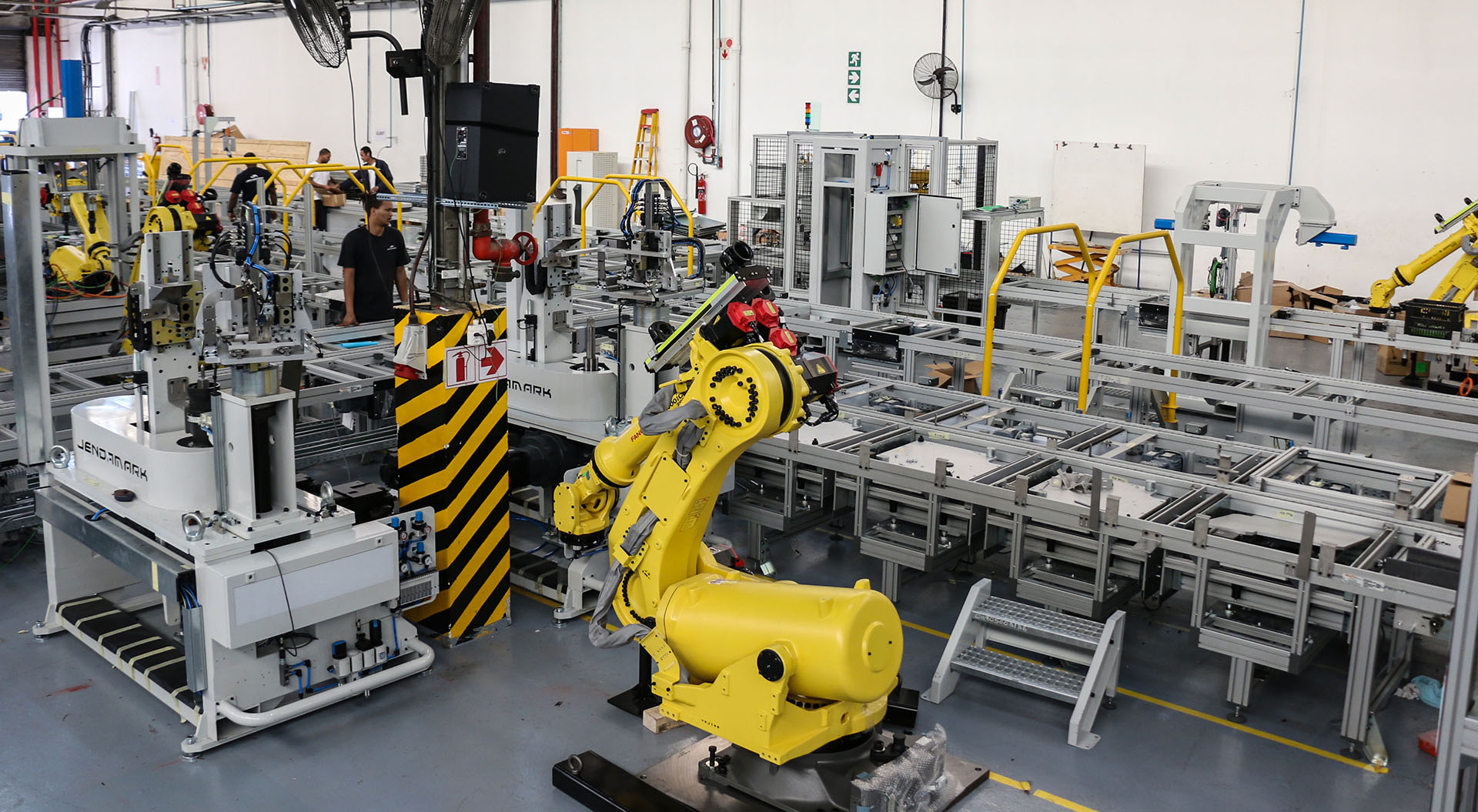
The customer had sourced multiple machines from various suppliers for their differential assembly facilities across the globe. This meant that ZF could not compare backlash measurement at their facility in China with the backlash measurement in the USA. Even when they were from the same machine builder, the machines differed because they were customised for a specific differential.
Our Building Block Methodology
Selecting an assembly line supplier can be daunting. While many machine builders are capable of producing high-quality machines, most projects are treated as once-off, and insights gained from previous projects are not used to inform subsequent ones.
Our building block approach aims to build the most modular and flexible machines, which can be configured and reconfigured to meet differing global production demands. It has helped customers save resources, mitigate risks, and, most importantly, avoid project-related stress.
We collaborate with our customer’s team to develop a fixed set of machines and processes that will serve as the standard building blocks for all future assembly lines. Once the building blocks have been established, the focus shifts to optimising essential line-specific requirements such as cycle time, floorspace and headcount.
Working together towards this shared goal of achieving long-term standardisation helps avoid technical and commercial decisions that cost more in the long run.
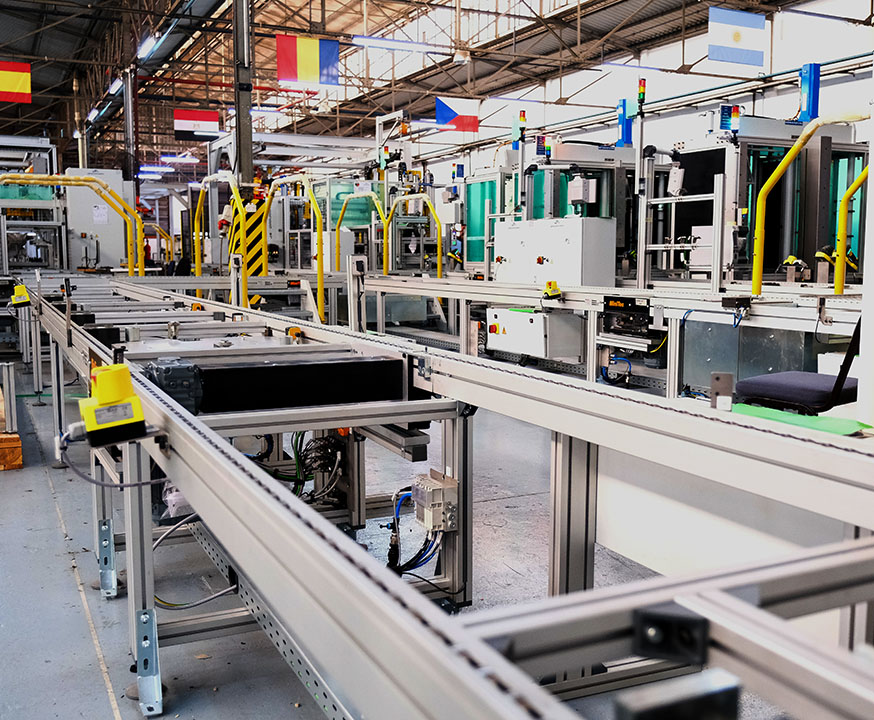
Our Solution
To address ZF’s global challenges, Jendamark developed a set of standard building block machines. These generic machines were designed to perform a particular process and could be adapted according to the tooling used.
With most of the software, mechanical design and process steps determined upfront for each machine, Jendamark could deliver these core building block machines for every new differential line project, and they would be the same for every ZF facility worldwide.
The complete assembly lines offered a standard but flexible solution comprising a mix of fully automated and manual stations.
Customer Benefits
Because the machines were co-developed with the customer’s experts, adopting lessons learnt from previous projects with multiple vendors, we were able to deliver best-in-class backlash and pinion nut tightening machines with a 15% cost saving.
- Reduced design time: A standard machine will require minimum design resulting in a reduced cost and quicker release time. Machines can be configured into various levels of automation.
- Faster delivery: Reduced assembly line delivery time from 18 to 12 months.
- Long-term savings: Time saved can be spent on optimising layouts, ergonomics and logistics planning.
- Reduced cost to add variants by 30%: Machines and pallets are co-developed with quicker, more flexible tool change and future part dimensions in mind.
- Increased machine reliability: Machines are tried and tested, with improvements made in a controlled and low-risk manner.
- Reduced learning curve: Once familiar with the standard machine, operators and technicians do not have to relearn a new machine for each project.
- Optimised number of operators: Key stations are automated regardless of location.
- Faster installation and ramp-up time: Familiar machines are installed and commissioned faster.
- Machines in stock: Can build up a store of standard machines to supply within weeks of requesting.
- Process standardisation: Process experts can manage, implement and deploy standardised assembly processes globally from a central planning team.
- Standard pricing for faster quoting times: Enables our customer to bid more effectively and accurately on new business.