Critical Assembly Processes
Applying the right specialised process to assemble your product is critical to its performance and overall quality.
- CRITICAL ASSEMBLY PROCESSES
Expert Technologies
Jendamark’s assembly systems feature a range of high-precision technologies.
Pressing
Whether you require small or large-scale precision pressing operations, our team delivers reliable, efficient solutions tailored to your specific needs, including monitoring force and displacement, and implementing specialised press force strategies.
Specialised pressing methods include:
- Manual arbour pressing
- Hydraulic pressing
- Servo pressing
- Hydro pneumatic pressing
For a wide range of components:
- Studs
- Tubes
- Bearings
- Pins
- Seals
- Dowels
- Shafts
- Rings
Tightening
Our precision tightening solutions ensure optimal performance and safety, using methods such as:
- Straight
- Torque
- Angle
- Yield tightening
Applications:
- Axle assemblies
Precise bolt tightening using synchronised yield methods - Ring gears
Accurate torque control for secure mounting - Engine mountings
Reliable tightening to prevent vibration and noise - Head and diff covers
Consistent sealing and performance - Ring covers
Secure attachment for critical components - Axle bolts
Consistent and controlled tightening for safety
We also offer pre-torque tightening and automatic tightening solutions to streamline your production processes and improve efficiency.
Gauging and measurement
Overview
Overview:
Our advanced gauging and measurement technologies can help you achieve higher levels of quality, efficiency, and productivity in your operations.
Specialised measuring methods include:
- Laser distance measurement
Accurate measurement of distances using laser technology - Laser displacement measurement
Precise measurement of surface displacement or deformation - Non-contact measurement
Measurement without physical contact, ideal for delicate or moving objects - Probe measurement
Contact-based measurement using probes for dimensional accuracy - Vision system measurement
Optical measurement using cameras and image processing for dimensional inspection and analysis
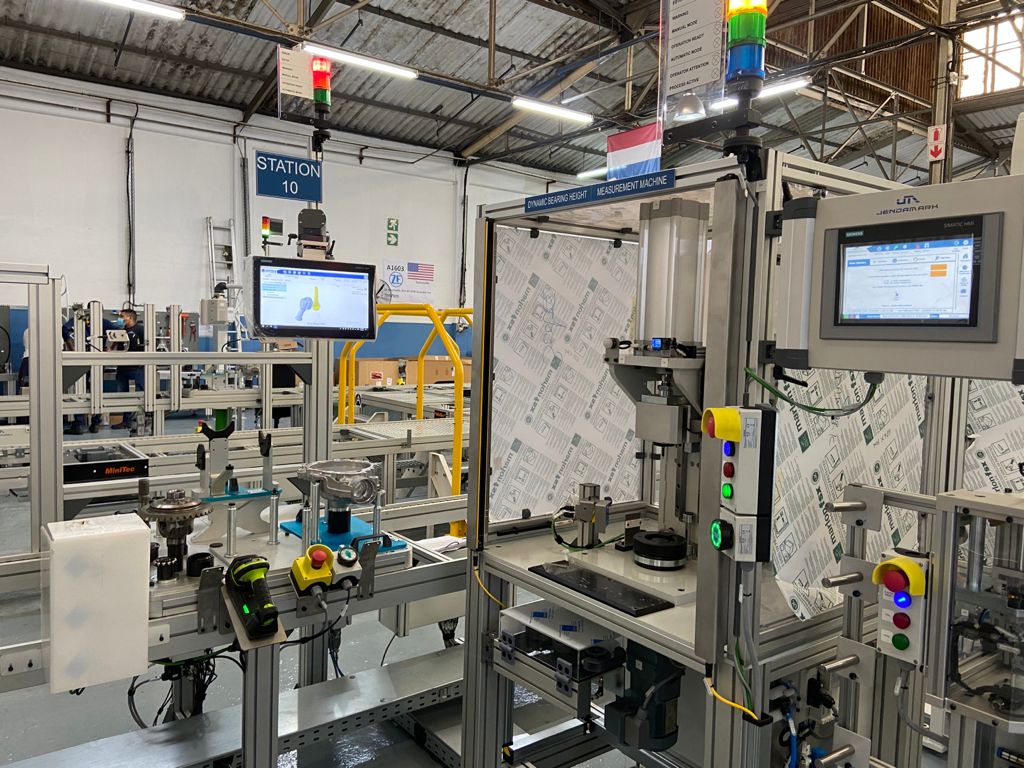
Industries:
- Manufacturing
Quality control, dimensional inspection, and process monitoring - Automotive
Assembly line inspection, component verification, and reverse engineering - Aerospace
Aircraft component inspection, dimensional verification, and tolerance analysis - Electronics
PCB inspection, component placement verification, and assembly line control - Research and development
Prototyping, material testing, and scientific experimentation
Benefits:
- Improved accuracy
Precise measurements for enhanced quality control - Increased efficiency
Faster inspection times and fewer errors - Enhanced productivity
Streamlined production processes and improved yields - Cost savings
Reduced scrap rates and rework costs
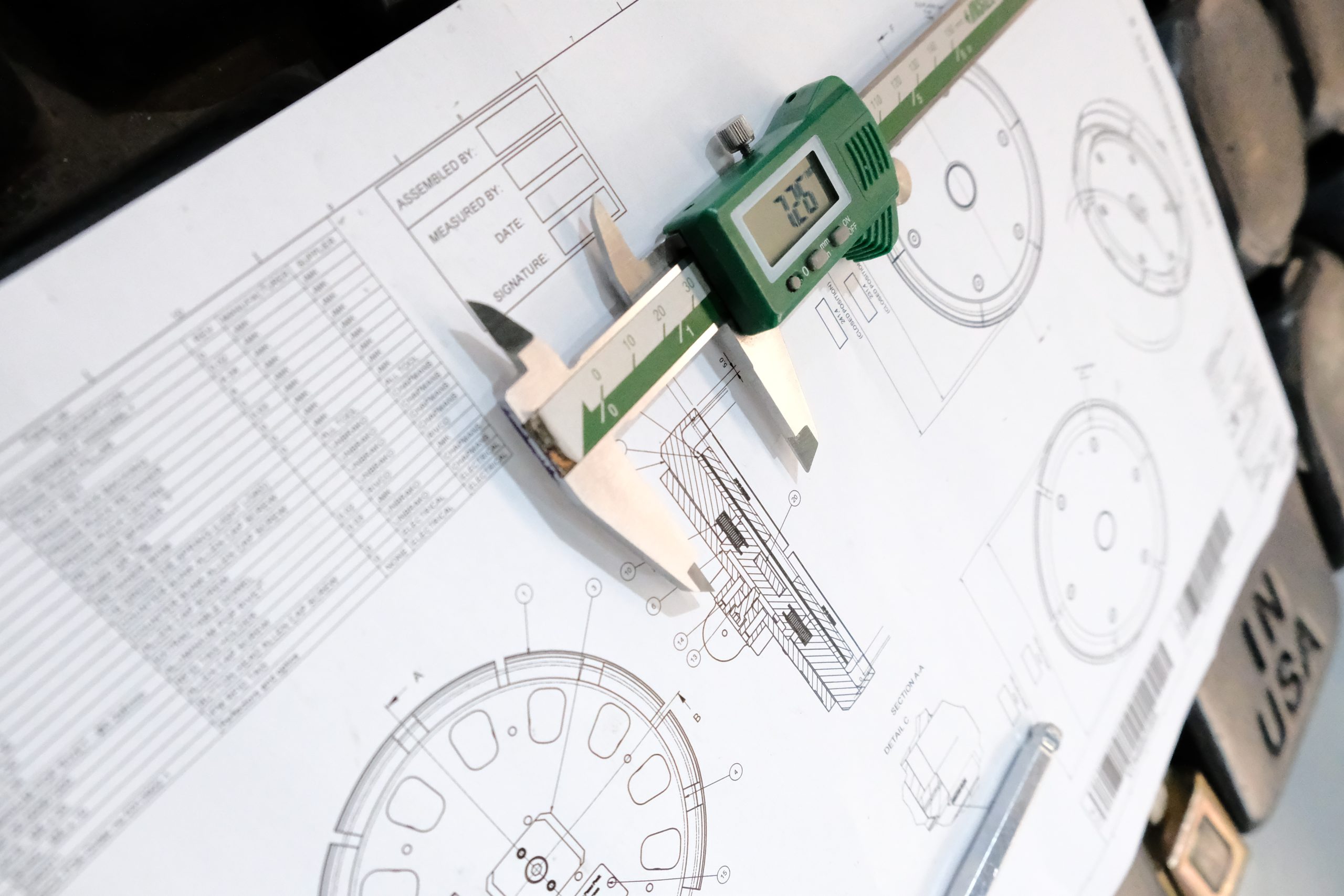
By using our precision gauging and runout measurement expertise, you can ensure the accuracy and reliability of your products.
Applications:
- Corner units
Measuring the runout of components on axle lines. - Pinion runout
Assessing the concentricity of a pinion gear. - Flange runout
Measuring the deviation of a flange face from a true plane. - Shaft runout
Evaluating the straightness and concentricity of a shaft.
Backlash Measurement
Backlash refers to the amount of play or clearance between two meshing gears or other moving parts. Accurate backlash measurement is crucial for ensuring proper operation, efficiency, and longevity of mechanical systems.
Why backlash measurement is important:
- Precision
Ensures that components fit together correctly and operate smoothly. - Efficiency
Reduces noise, vibration, and energy loss. - Durability
Prevents excessive wear and tear on moving parts.
Our specialised techniques include:
- 3-point measurement
This method involves measuring the backlash at three points along the gear mesh to obtain an average value. - Manual audit
A more traditional approach where backlash is measured manually using tools like feeler gauges or dial indicators. - Dynamic backlash measuring
This technique uses advanced equipment to measure backlash while the system is in motion, providing real-time data on clearance variations.
Applications:
- Automotive
Gearboxes, differentials, steering systems - Industrial machinery
Gear drives, gearboxes, machine tools - Aerospace
Aircraft components, landing gear - Robotics
Robotic arms, joint mechanisms
Gear Friction Measurement
Our expertise lies in measuring gear friction using specialised tools and techniques. By precisely measuring gear friction and applying appropriate torque, we help ensure the efficiency and reliability of your gear-driven components.
Services offered:
- Torque measurement
Accurately measure the torque required to rotate gears. - Pinion nut tightening
Apply the correct torque to securely tighten pinion nuts. - Preload application
We understand the impact of preload on torque and ensure optimal performance.
Applications:
- Differential assemblies
- Gearboxes
- Other gear-based systems
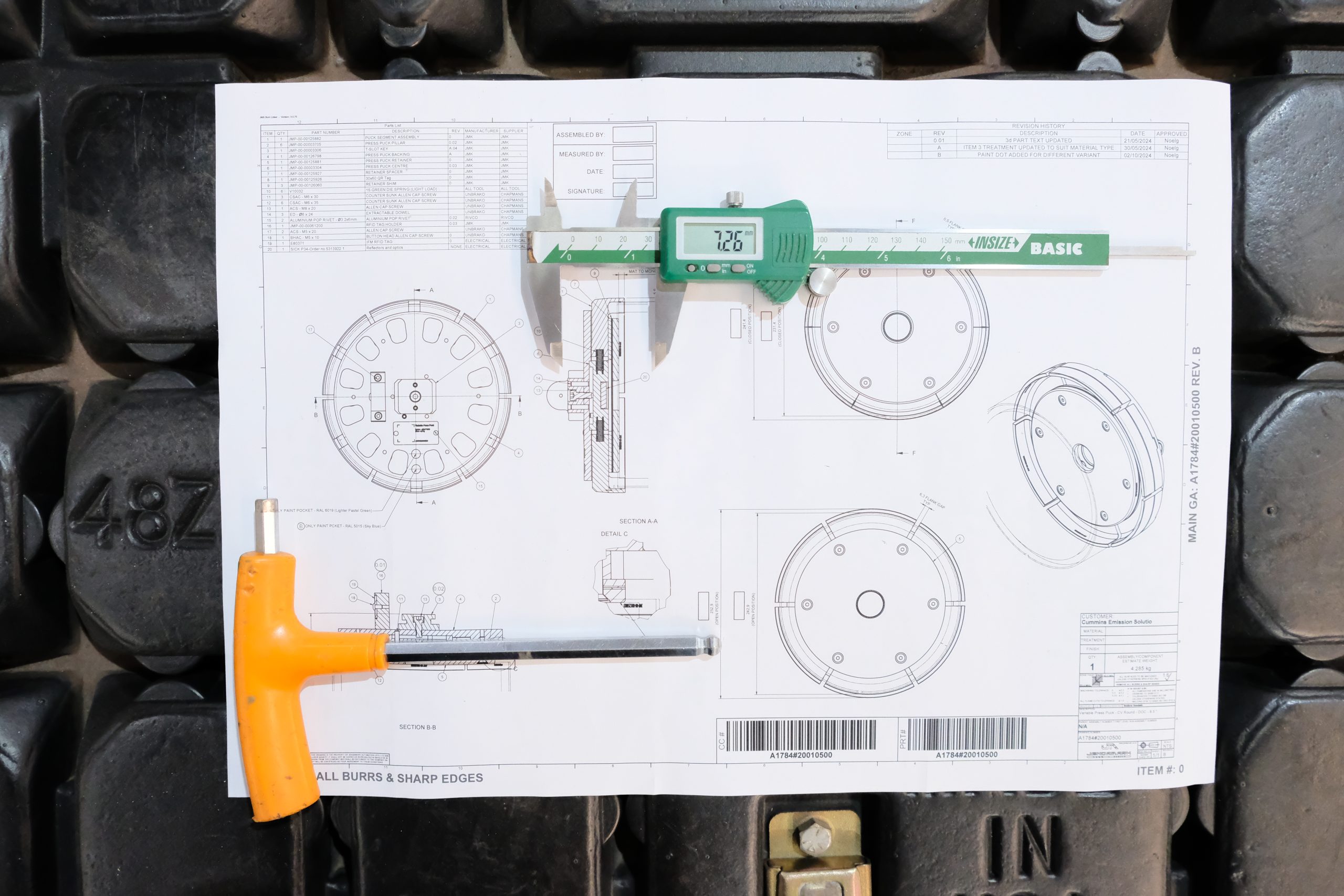
Torque To Turn
Gear friction and torque measurement is a critical aspect for ensuring optimal performance, efficiency, reliability and longevity in mechanical systems.
Our specialised techniques include:
- Torque to rotate
Measuring the torque required to rotate a gear or gear pair. - Pinion nut tightening
Assessing the torque applied to tighten the pinion nut, which affects gear meshing and performance. - Spinning and measuring torque
Determining the torque generated during gear rotation, providing insights into friction and efficiency.
Why is gear friction measurement important?
- Efficiency
Reduces energy loss and improves overall system performance. - Durability
Prevents excessive wear and tear on gear components. - Noise reduction
Minimises noise and vibration caused by friction. - Optimisation
Enables fine-tuning of gear design and operation.
Applications:
- Automotive
Gearboxes, differentials, steering systems - Industrial machinery
Gear drives, gearboxes, machine tools - Aerospace
Aircraft components, landing gear - Robotics
Robotic arms, joint mechanisms
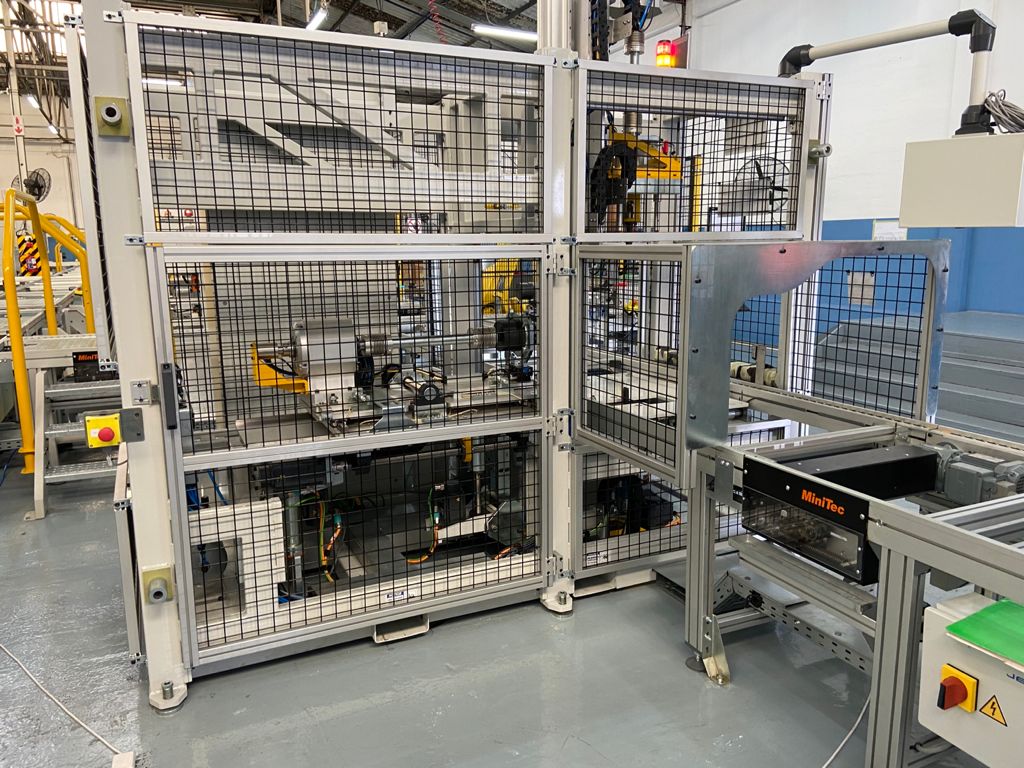
Leak testing
We specialise in a variety of leak testing methods, including pressure decay tests.
Applications:
- Housing components
- End-of-line assemblies
- Post-welding inspection
- Weld integrity verification
- Component sealing checks
- Flaw detection
- Sample testing
Robotic sealant application
We specialise in robotic sealant applications, including :
- Dosing systems
- Glue dispensing
- Glue spraying
- Electric module sealing
- Gasket sealing for components like differentials and engine lines
Our robotic sealing capabilities cover a wide range of applications, such as spot sealing, bead sealing, structural sealing, and cosmetic sealing.
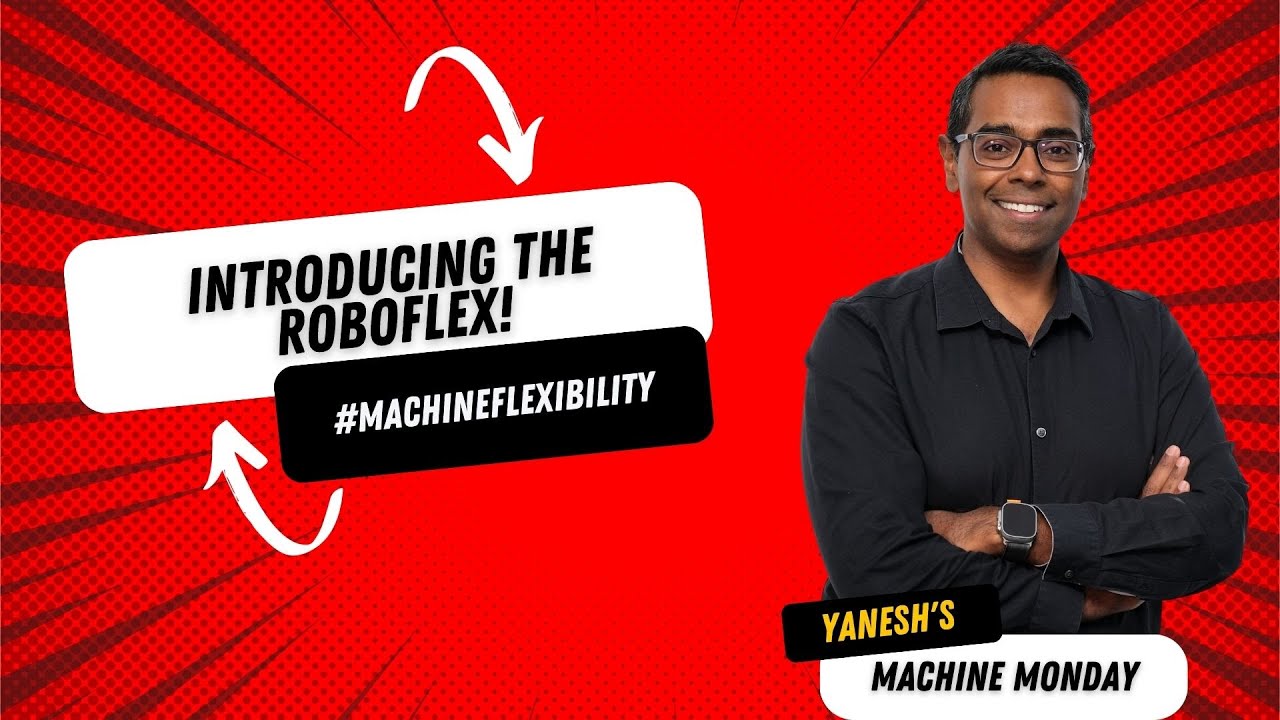
Process planning
We specialise in process planning, a critical aspect of manufacturing that involves analysing and optimising production processes. By leveraging our process planning expertise, you can streamline your production, reduce costs, and improve overall efficiency.
Our expertise includes:
- Cycle time optimisation
Reducing the time required to complete a process. - Bottleneck reduction
Identifying and addressing constraints that slow down production. - Line balancing
Ensuring a smooth flow of work through the production line. - Operator efficiency optimisation
Improving the productivity and effectiveness of your workforce. - Layout optimisation
Arranging equipment and workstations for maximum efficiency. - Cycle time calculation and assessment
Analysing and evaluating process times.
Traceability solutions
Our traceability solutions leverage advanced technologies like laser scanning, direct part marking, and barcode scanning to link data directly to components. This ensures complete traceability throughout the product lifecycle, allowing you to gain valuable insights into your operations, improve product quality, and meet regulatory requirements.
- Laser scanning
High-precision scanning for detailed component inspection and tracking. - Direct part marking
Permanent marking of part information directly onto the component. - Scanning
Efficiently capturing and storing data from barcodes, QR codes, and other markers. - Barcoding
Implementing barcode systems for easy identification and tracking. - Pin stamping
Applying permanent marks or identification numbers using pin stamping techniques. - Linking data to components
Connecting component data to relevant information, such as manufacturing records, quality control results, and maintenance history.
Auto and manual part handling
We specialise in a variety of part handling technologies, including:
- Grippers
- Manipulators
- Robots
- Gantry systems
- Lift assist devices
Applications:
- Assembly lines
Moving components from one station to another. - Material handling
Transporting raw materials, finished products, and work-in-progress. - Machine tending
Loading and unloading parts from machines. - Quality inspection
Handling parts for inspection and testing. - Welding and assembly
Holding and positioning parts for welding and assembly processes. - Packaging
Packaging finished products for shipment.
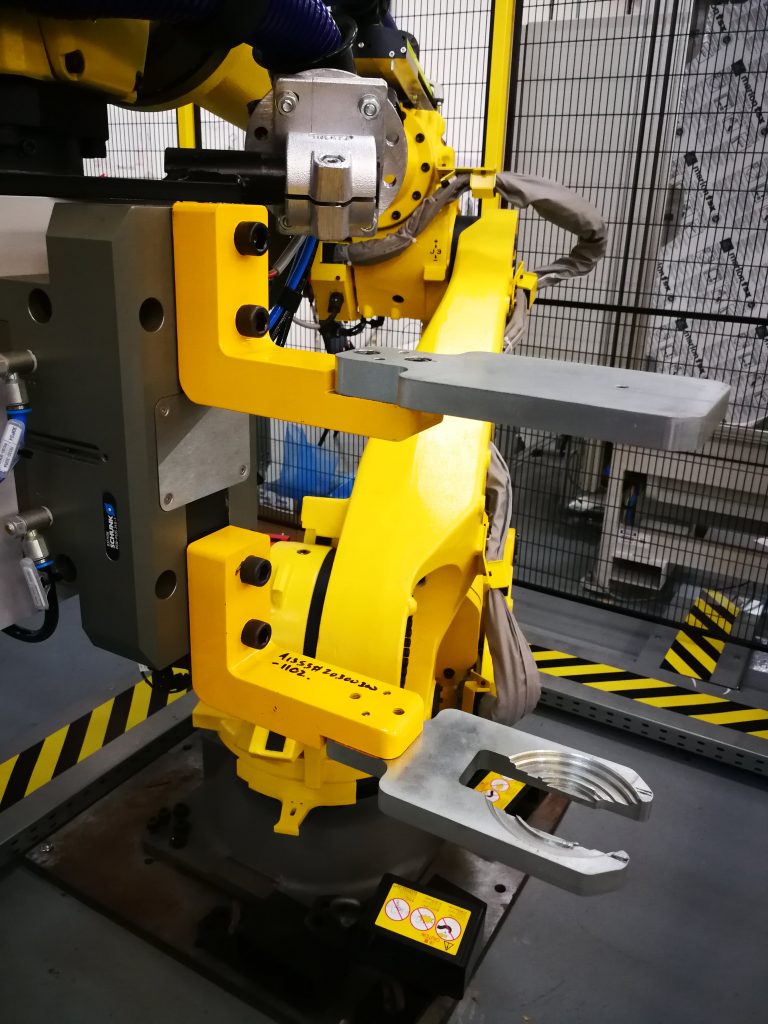
- AREAS OF EXPERTISE
EV Technologies
Jendamark’s assembly systems feature a range of industry-leading technologies, and we specialise in these high-precision solutions.
Polarity checking
Polarity checking ensures that the electrical connections (positive and negative terminals) are correctly aligned or arranged when assembling a battery pack. It verifies that the cells and the overall pack are connected in such a way that the current flows in the correct direction.
Purpose:
- Prevent reverse polarity, which can cause short circuits, inefficiency, or damage to battery cells.
- Ensure the correct assembly of the battery pack for functionality and safety.
- Avoid misconnection issues that could potentially lead to fires, overheating, or equipment failure.
Benefits:
- Safety: Correct polarity ensures that the battery pack will function safely and efficiently. Reverse polarity could cause short circuits, damage, or even thermal runaway.
- Reliability: Verifying polarity prevents the risk of electrical issues, ensuring the pack performs as intended in its application.
- Longer lifespan: Proper polarity prevents premature wear or failure of battery cells or the pack due to incorrect connections.
Technology used:
- Automated testing systems: These systems are equipped with voltage measurement devices or continuity testers. They scan the entire battery pack for proper polarity and alert operators to any misalignment.
- Advanced vision systems: Systems with AI can be programmed to visually inspect the orientation of cells, tabs, and connectors in a battery pack. These systems can quickly verify that the correct polarity is established.
Laser Tab Welding
Laser tab welding is a process used to create precise and strong electrical connections between the battery cells and the interconnecting tabs (usually made of nickel or other conductive metals). This method uses focused laser energy to melt and join the metal tabs to the battery cell terminals, ensuring a high-quality, low-resistance connection.
Purpose:
- Efficient and precise welding: Ensures a strong, high-quality weld between the battery cell and connecting tab.
- Reduced risk of damage: Laser welding is a non-contact, localised heat method that minimises the risk of damaging sensitive battery cells during the welding process.
- Consistent and repeatable results: Laser welding ensures uniformity in the welds, which is critical for the performance, reliability, and safety of the battery pack
Benefits:
- High precision: The accuracy ensures that the welds are consistently strong and well-formed.
- Reduced thermal damage: Unlike traditional welding methods, laser welding has a small heat-affected zone, which reduces the risk of thermal damage to the battery cells and other components.
- Minimal material distortion: The localised heat generated by the laser minimises material distortion, preserving the integrity of the cell and the tab.
- Strong, reliable joints: Laser welding creates strong, low-resistance joints that are capable of handling the high currents often required in battery packs.
- Non-contact process: Laser welding is a non-contact process, meaning there is less mechanical stress on the materials, leading to more reliable welds.
- Speed and automation: Laser welding can be automated for high-speed production, leading to faster manufacturing cycles and reduced labour costs.
Technology used:
- Fibre laser welding systems: These are commonly used for high precision, as they deliver concentrated, high-power laser beams. Fibre lasers are known for their efficiency and reliability in welding thin materials like the metal tabs.
- CO2 lasers: Older but still effective, CO2 lasers can also be used in tab welding, though fibre lasers are more common for modern battery production lines.
- Robotic welding arms: Automated robotic arms equipped with lasers move the laser precisely and repeatedly over the weld points. These robots can be programmed for consistent, high-accuracy welding across multiple cells.
- Vision systems: Integrated vision systems may be used to align the tab and cell terminal accurately before welding. They ensure that the laser hits the correct welding location each time, improving consistency.
High potential (hipot) testing
High potential (hipot) testing is an electrical safety test used to verify the insulation integrity of a battery pack. It involves applying a high-voltage potential (much higher than the normal operating voltage) between the battery’s internal components and the ground (or casing) to ensure there are no electrical leaks or insulation failures.
Purpose:
- Safety assurance: To ensure the battery pack’s insulation can withstand higher voltages than it would normally encounter in operation, preventing electric shocks, fires, or other safety hazards.
- Insulation integrity: To ensure no unintended electrical paths or connections (leakage current) exist that could lead to failures.
- Compliance with standards: To meet international safety standards such as IEC 61010, UL, or ISO that require testing for electrical insulation and safety.
Benefits:
- Safety assurance: The primary benefit is ensuring that the battery pack is safe for use by preventing electrical shocks, short circuits, or fires that could result from insulation failures.
- Quality control: Helps identify faulty insulation in battery packs that could lead to early failure in real-world use, thereby improving the overall product quality.
- Regulatory compliance: Helps manufacturers meet regulatory safety requirements, ensuring the product adheres to industry standards and avoiding potential legal and financial consequences from unsafe products.
- Reliability: Increases the reliability and longevity of the battery pack by ensuring its insulation can withstand potential voltage surges and environmental stress.
Technology used:
- Hipot tester: Modern testers can provide precise readings of leakage current and display results in real-time, sometimes with advanced features like data logging.
- Automated test systems: Can integrate hipot testing into the production line, allowing multiple packs to be tested in succession with minimal human intervention. This is ideal for high-volume production environments.
Open-circuit voltage and internal resistance testing
Open-circuit voltage (OCV) testing measures the voltage of a battery or battery pack when it is not connected to any load application.
Purpose:
- Cell sorting: Based on the OCV and IR data, cells can be sorted into different grades.
- Confirm correct cell configuration: To ensure that the cells in the battery pack are of the same grade or type.
- Safety check: To detect any significant issues such as undercharged cells or manufacturing defects that could lead to failure during operation.
Benefits:
- Performance validation: Helps confirm that the battery can provide the necessary voltage when it is placed in service, minimising the risk of performance issues later.
- Early fault detection: Identifies faulty or undercharged cells or other issues in the early stages of production, allowing for corrective actions before the battery reaches the consumer.
- Consistency: Helps ensure that all battery packs are within the required voltage specifications, ensuring consistency across production batches.
- Safety: Prevents potential issues caused by faulty or mismatched cell voltages that could lead to overheating, malfunction, or safety hazards.
- Consistency: Helps ensure that all battery packs are within the required voltage specifications, ensuring consistency across production batches.
- Safety: Prevents potential issues caused by faulty or mismatched cell voltages that could lead to overheating, malfunction, or safety hazards.
Technology used:
- Digital multimeters or voltmeters: High-precision multimeters are necessary for highly accurate measurements, particularly in high-precision applications such as electric vehicles or medical devices.
- Automated testing systems: Equipment integrated into the assembly line can measure the OCV for large batches of battery packs efficiently. The automated system can compare the OCV against the expected value and flag any discrepancies for further inspection.
- Data logging systems: In some production lines, data logging systems are used to track OCV measurements over time. This ensures that the voltage readings are recorded for quality control and traceability purposes.
- Thermal management systems: If the battery pack has been recently charged or discharged, some packs may require a short resting period to allow the voltage to stabilise. In such cases, cooling or thermal management systems can be used to bring the battery pack to a safe testing temperature.
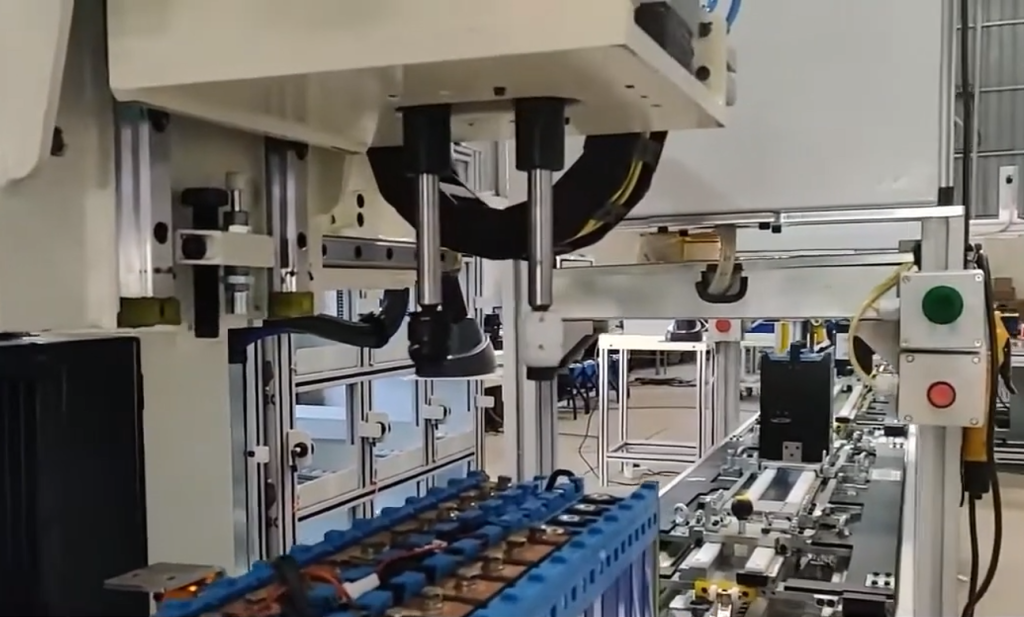
Build high-quality EV components
See how our expert EV technologies help to deliver industry-leading electric vehicle component assembly solutions.