In-house Processes
Specialised Departments
Jendamark maintains the highest possible quality standards by retaining control of a number of core development, production and testing processes in-house through our specialised departments.
Research and Development
In the fast-moving automation industry, the rate of change of technology is very high. At Jendamark, research and development (R&D) plays a critical, cross-functional role in delivering innovative solutions – every step of the way.
A team of experienced electrical and mechanical engineers assists our customers to find better, more efficient and cost-effective ways of achieving their production goals.
This technical support team works with the sales and design departments to find practical ways to refine processes, accommodate changing production volumes and improve outcomes, which informs the overall design.
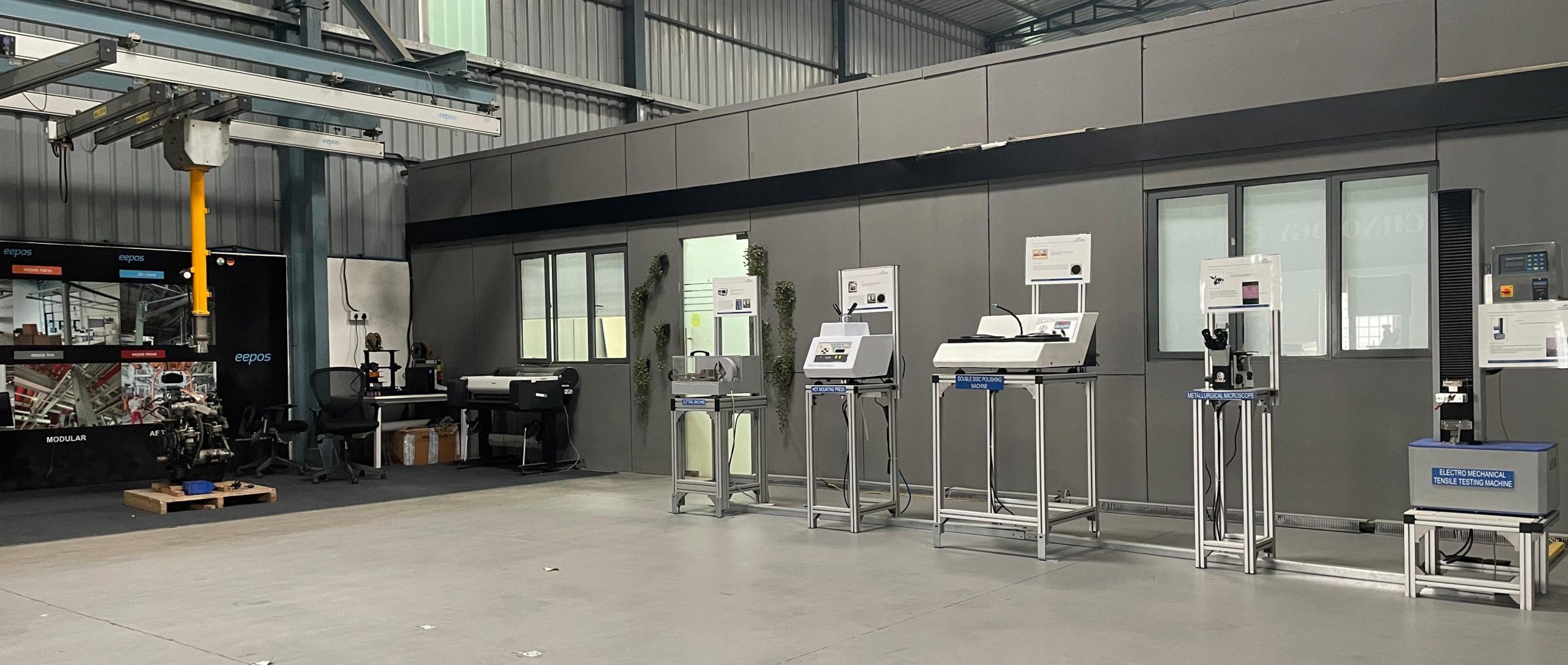
Standardisation
- Establish consistent design standards for Jendamark machines to ensure uniformity and modularity across similar machine types.
- Develop standardised components and part libraries to reduce repetitive design efforts and enhance efficiency.
- Maintain documentation templates and reusable design elements for future projects.
Conceptualisation
- Engage with the customer to understand and validate the project concept.
- Facilitate brainstorming sessions to explore innovative solutions with a focus on sustainable practices, and integrating 3D printing technologies into design processes.
- Provide technical consultation to ensure concepts are practical and aligned with capabilities.
Feasibility and risk analysis
- Conduct feasibility studies covering technical viability, budget, timeline, and resource requirements.
- Identify potential risks and develop mitigation strategies.
- Collaborate with production, quality, procurement, and service teams early to ensure design practicality and smooth downstream execution.
Here is how we do it:
In-depth assessment
- Visit customer sites to evaluate existing systems and gather insights on operational conditions.
- Collect and analyse customer feedback to identify pain points and improvement areas.
Prototyping and validation
- Develop physical or digital prototypes to test core design aspects.
- Use simulations or trial runs to validate key functionalities before full-scale development.
- Analyse performance data to support design decisions and minimize risks of late changes.
Partner identification
- Proactively identify and establish partnerships with new design collaborators and suppliers to enhance our design capabilities and expand our network.
- Create a structured knowledge base for future reference, onboarding, and continuous learning across teams.
Continuous improvement
- Revisit and refine design processes to incorporate lessons learned and emerging best practices.
- Implement customer feedback into future designs to ensure ongoing product and process improvement.
- Monitor post-deployment performance to capture long-term insights.
Precision Machine Shop
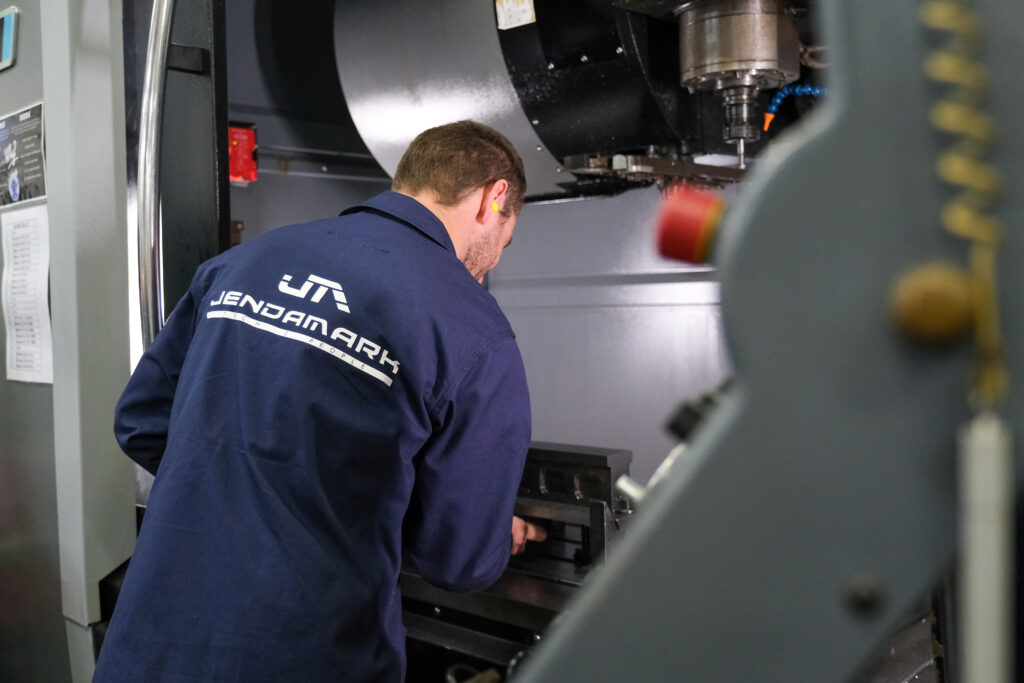
Jendamark believes that the machining of parts and tools is fundamental to the overall performance of the machines we build for our customers. Therefore, we have invested in expanding our precision machine shop, which stands among the most precise and accurate in the world.
We pride ourselves on manufacturing only the highest quality parts with the lowest annual scrap rates.
In South Africa, we have developed our own four-year, in-house apprenticeship programme, endorsed by the Department of Higher Education and Training, to ensure that we build a talent pool of artisans who do things the Jendamark way.
Metrology Department
Testing and measuring is a critical part of the manufacturing process. Jendamark’s in-house metrology department plays a key verification role in confirming that any manufactured parts or tools used on our assembly lines – whether produced by our precision machine shop or by a supplier – have been correctly and accurately made.
Jendamark goes beyond simply manufacturing a tool according to the supplied design.
We put the tool through its paces, testing it with the required materials and optimising the tool until it behaves in a highly repeatable way.
This version is then scanned and becomes the final drawing. Should a customer break a segment of a tool during their manufacturing process, our goal is to replace it seamlessly, so that the customer has the best chance of continuing production exactly where they left off.
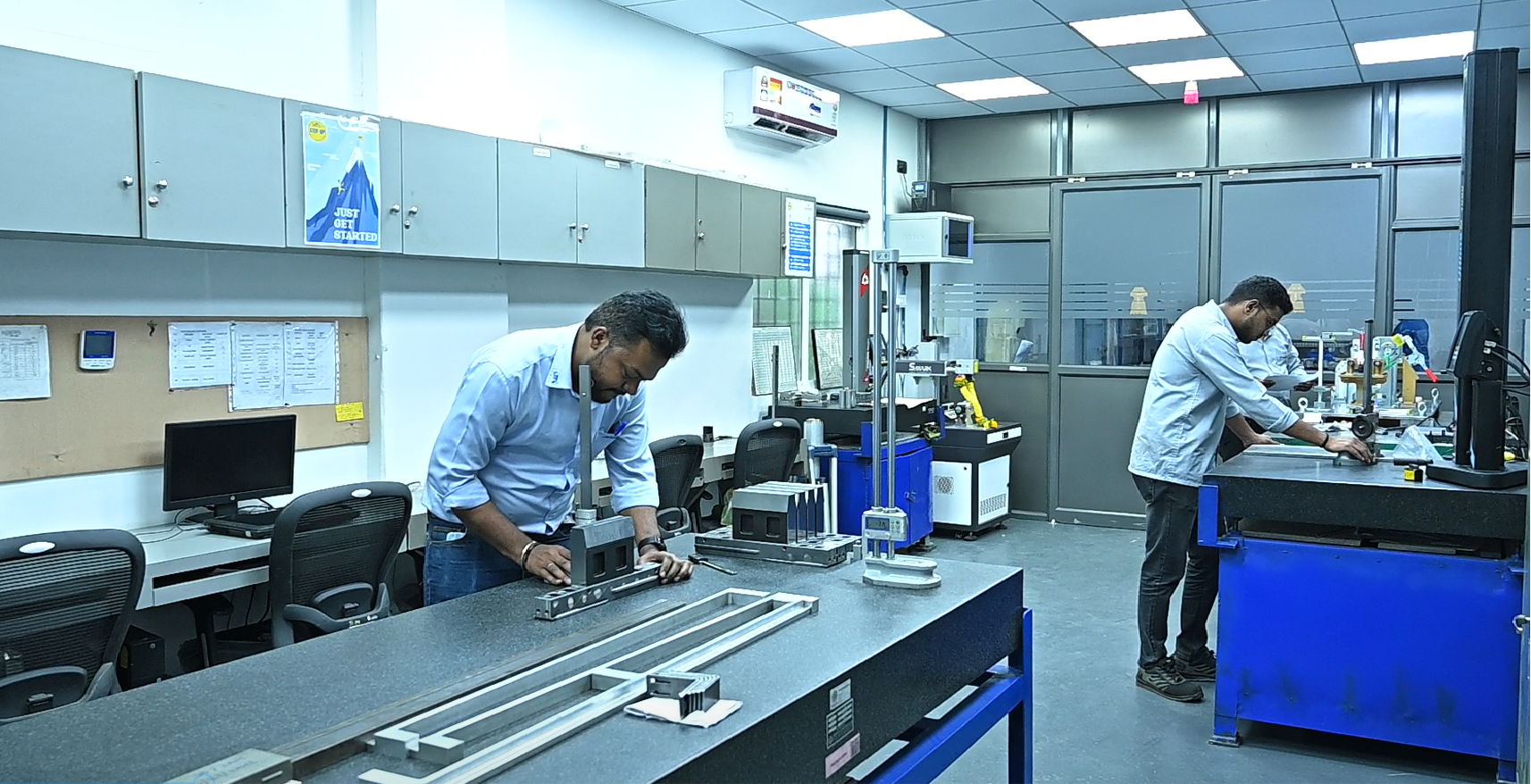
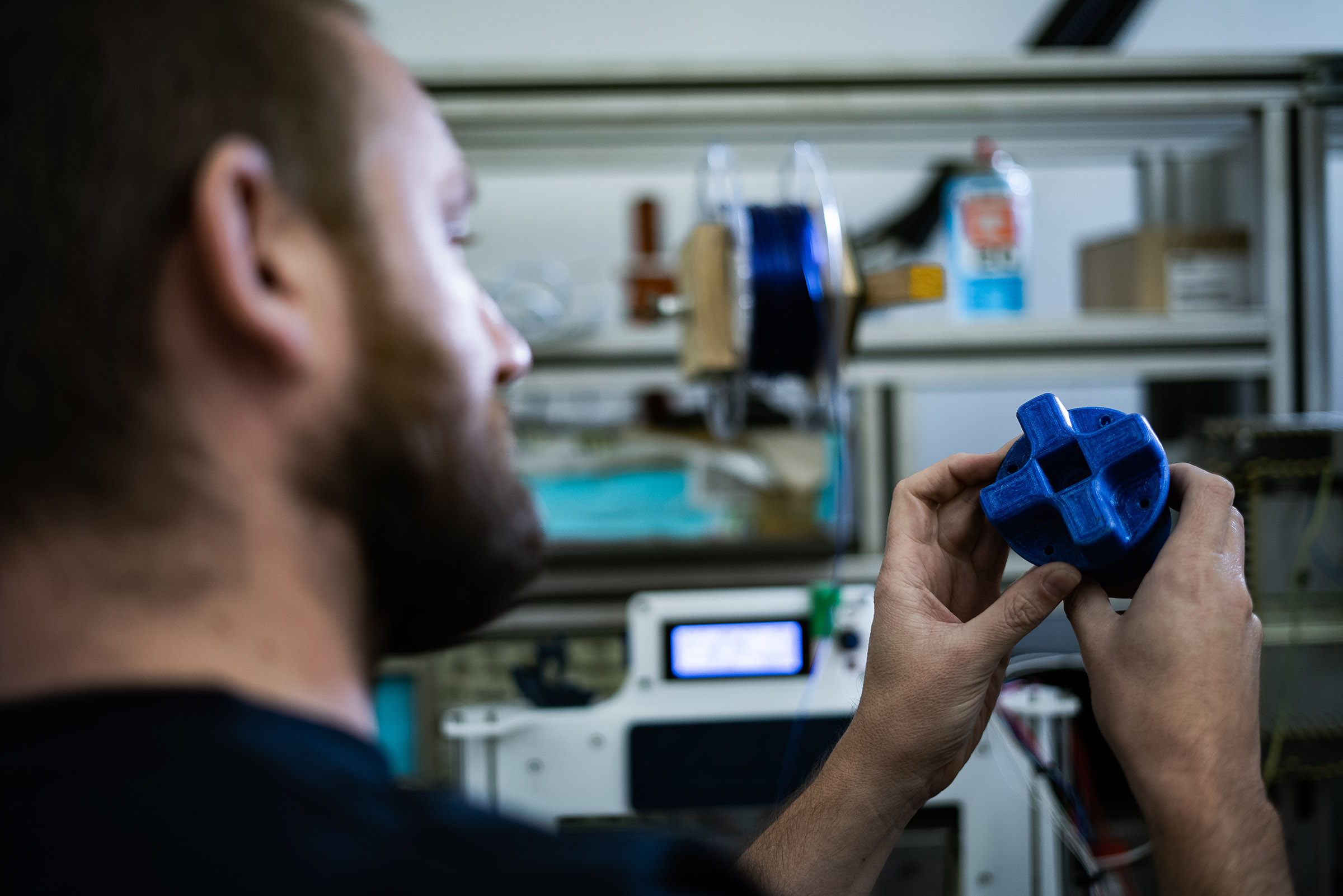
Critical assembly processes
Our specialised departments play an important role in developing and implementing our high-precision, expert technologies.