New Energy
Electric Vehicles
Jendamark provides customised assembly line and testing solutions to leading EV manufacturers. These range from component-level lines for battery packs, motors, rotors, transmissions and micro controller units (MCU) to solutions for full vehicle assembly.
Manufactured
EV Component
Assembly Lines
Assisted
EV OEMs and
Tier 1 Suppliers
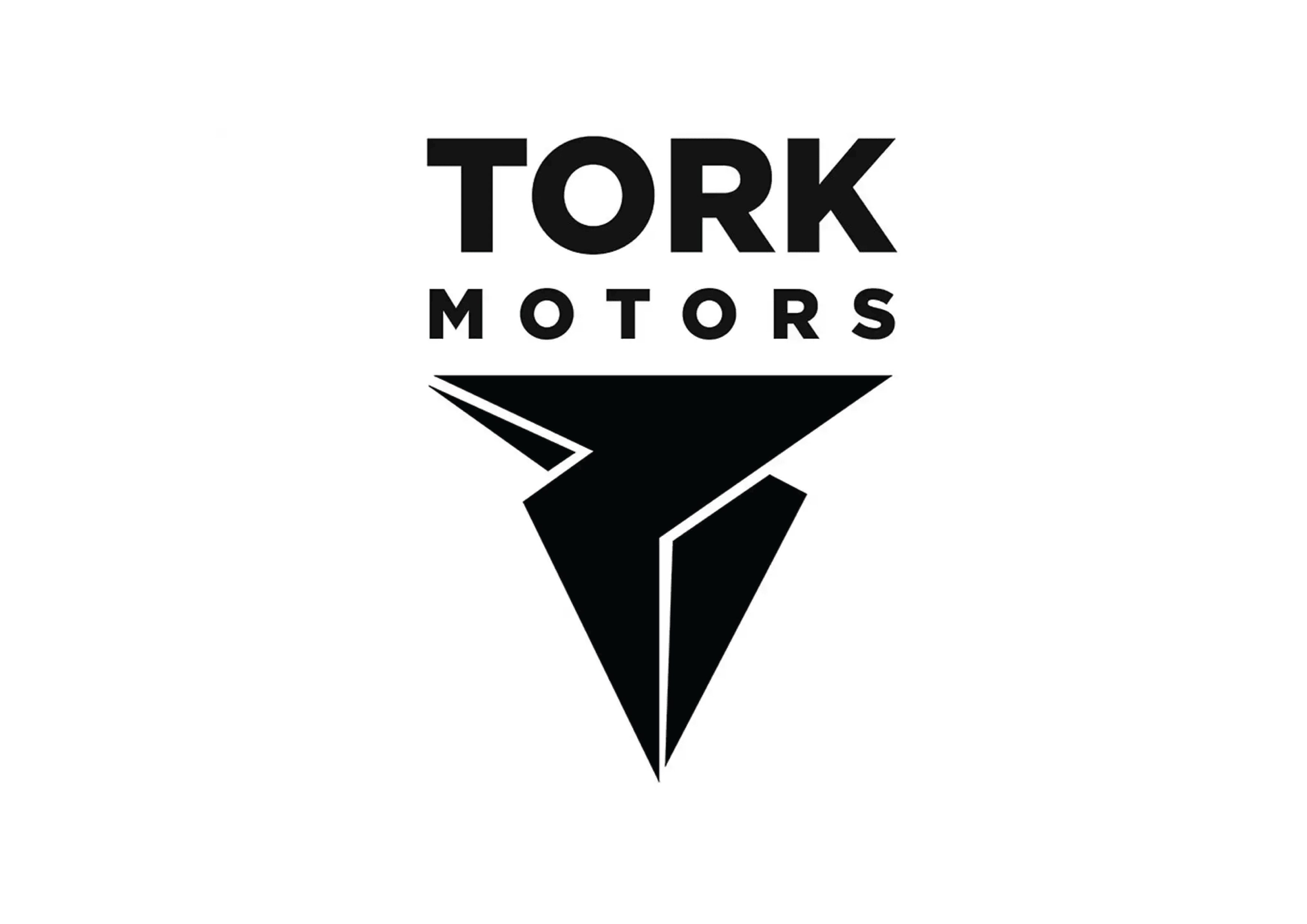
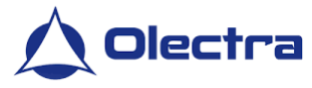
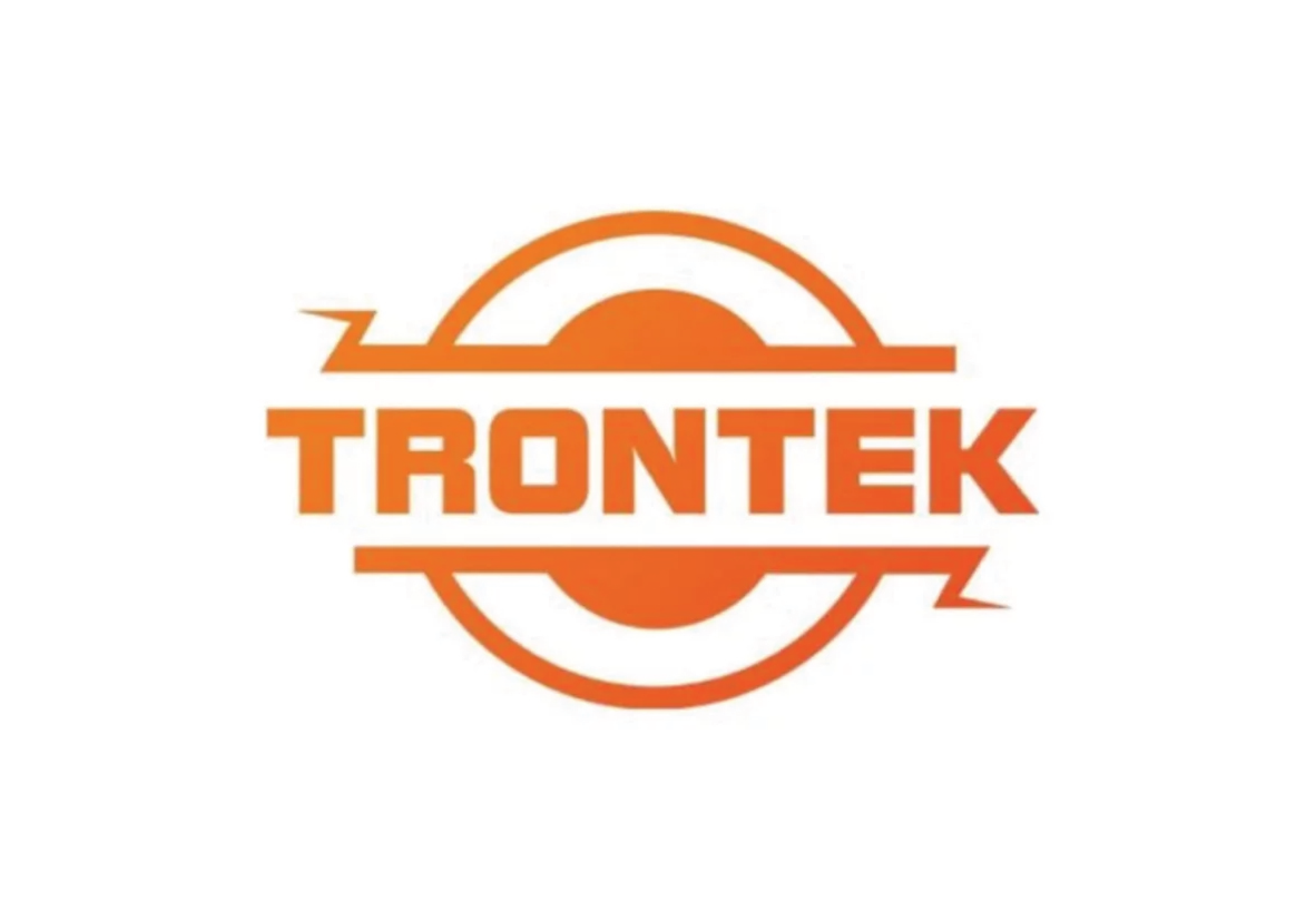
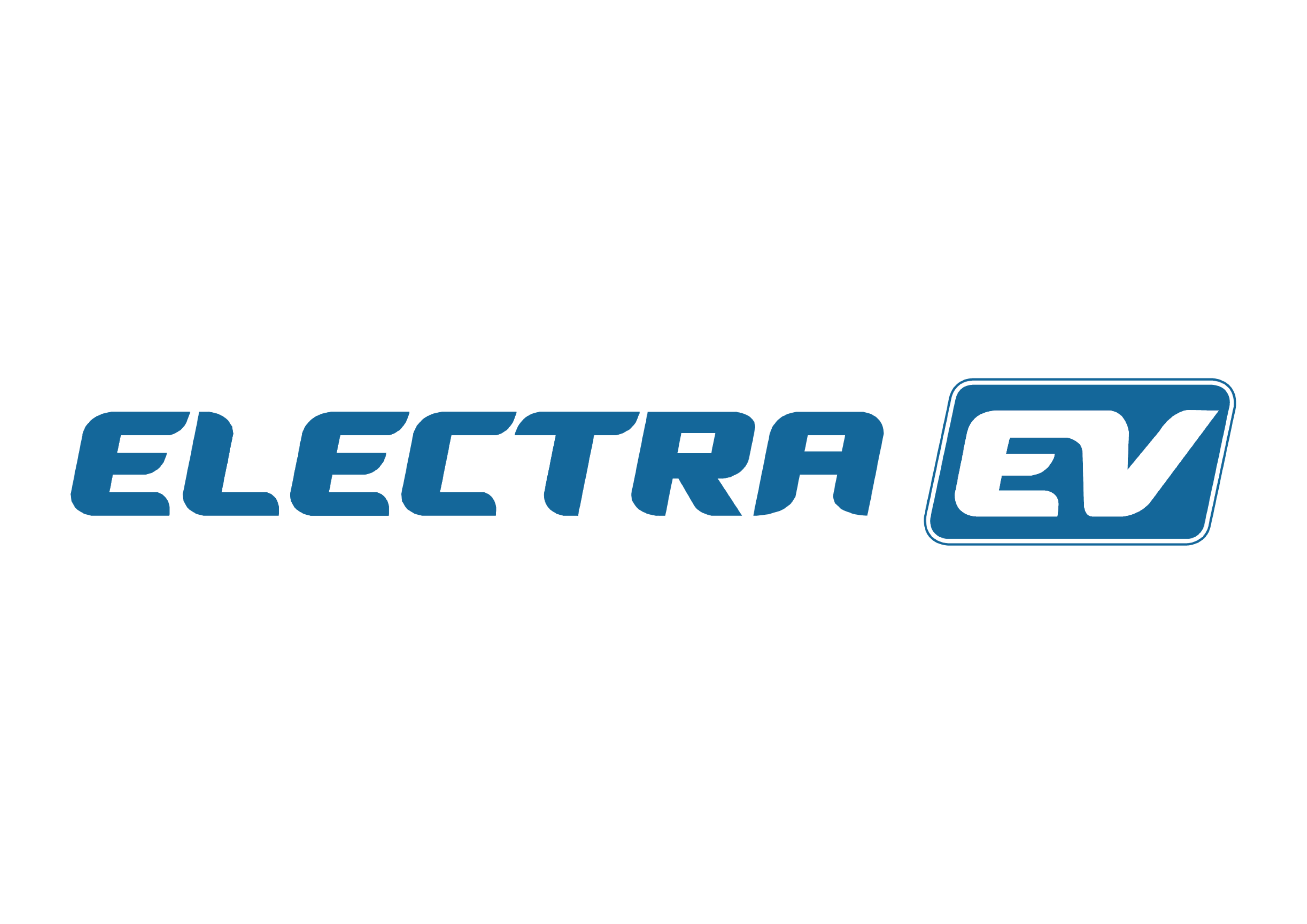
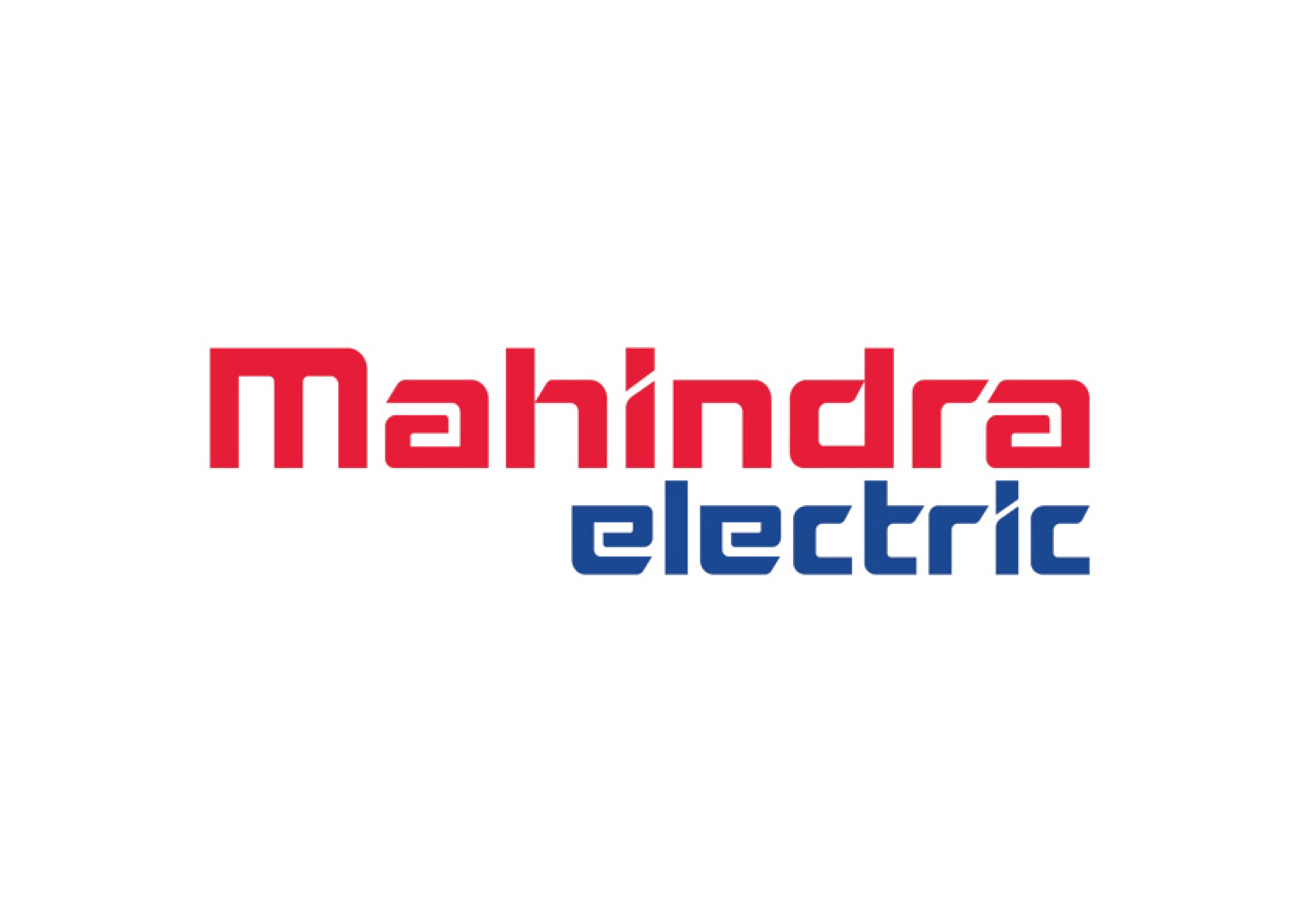
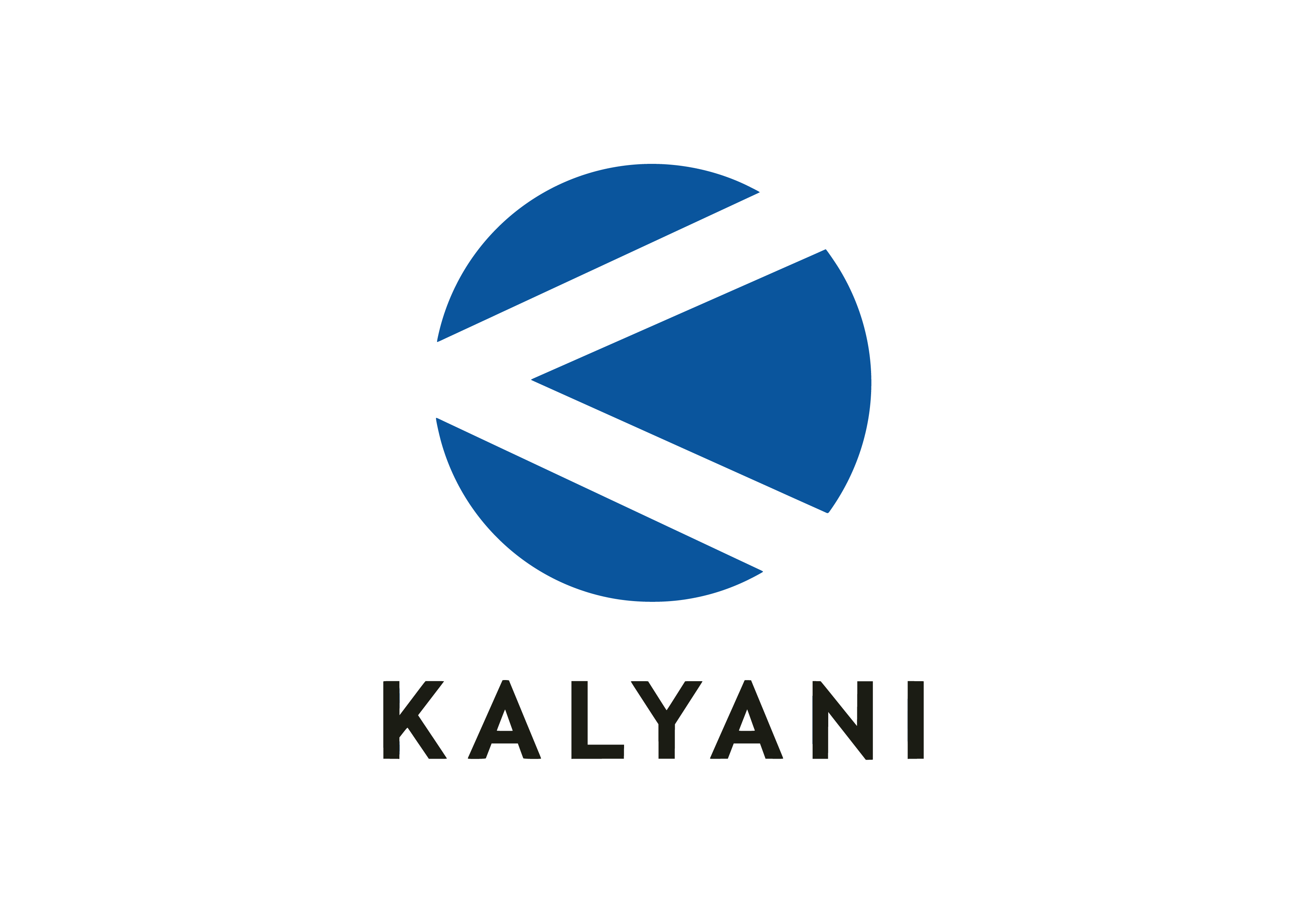
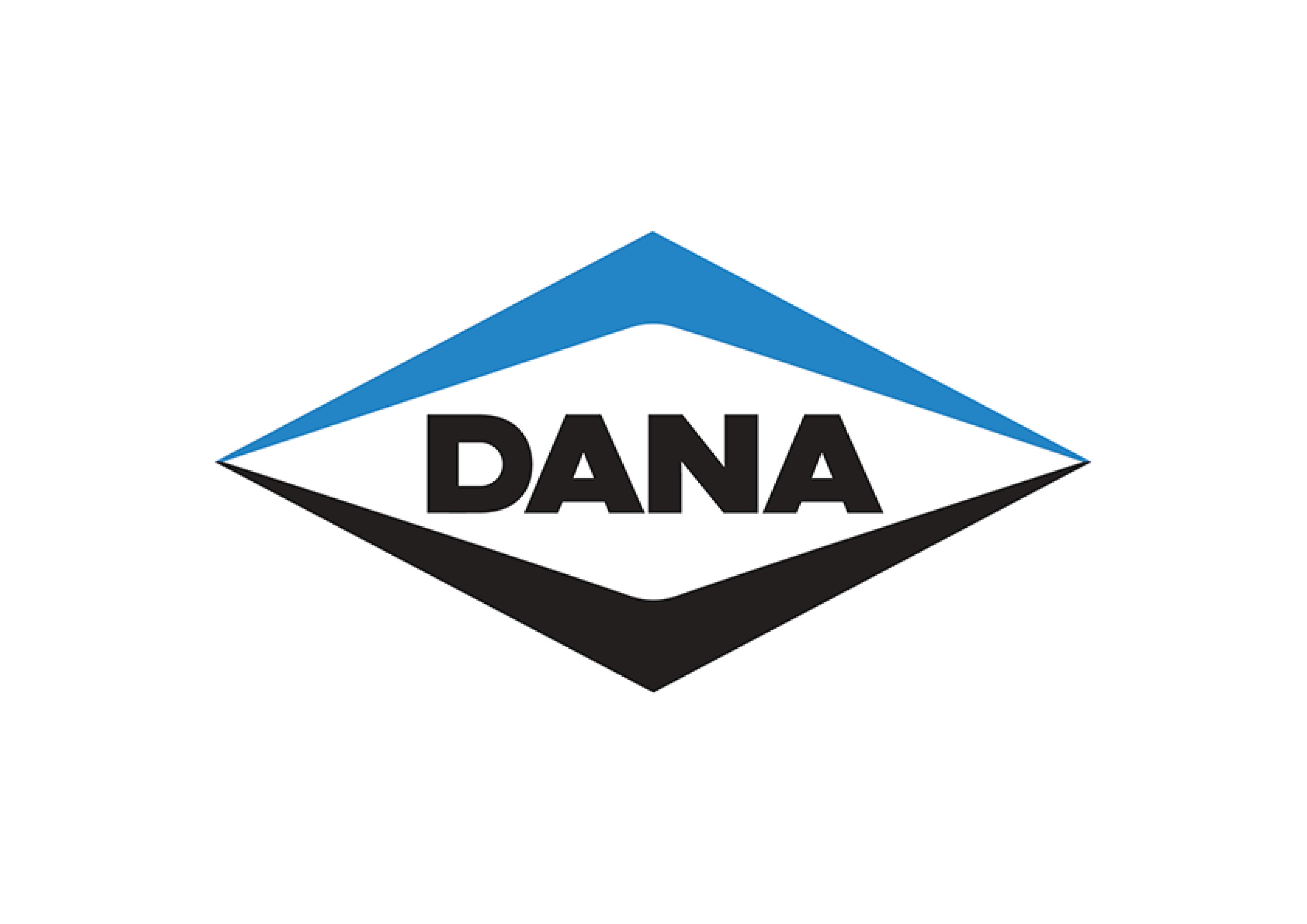
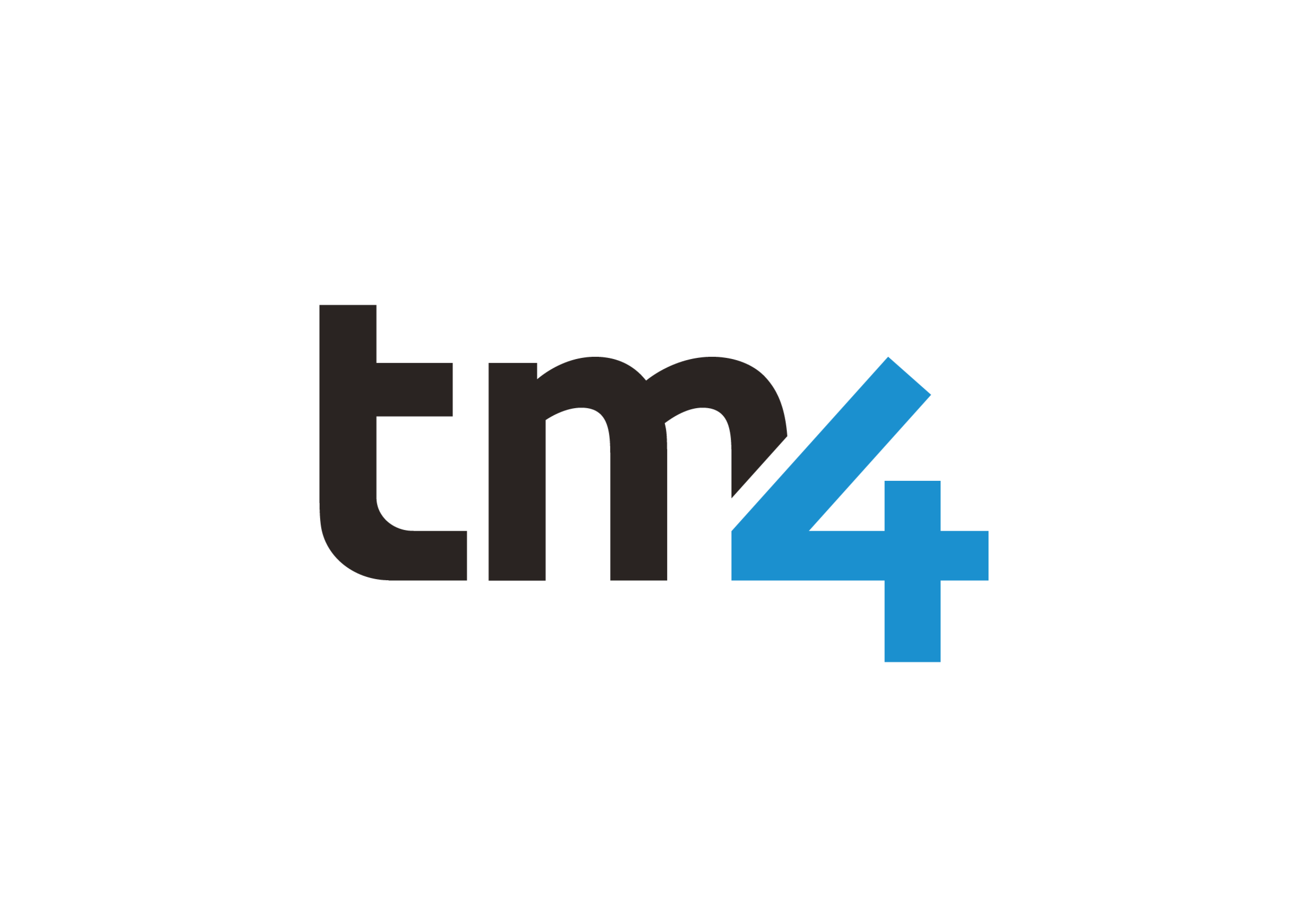
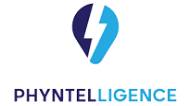
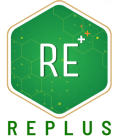
Explore our EV component assembly line solutions
Battery Pack Assembly
Battery pack assembly involves putting together a power pack, or cluster of batteries, used to power an electric vehicle.
A typical battery pack assembly line is broken down into 3 sections:
- Cell inspection
- Module line
- Pack line
Learn how our expert technologies ensure a safe, high-precision battery pack assembly process.
Explore the various assembly lines we have built by expanding the boxes below:
Prismatic Battery Assembly Line (Type 1)
Manufactured and delivered to one of India’s most valuable and well-recognised car manufacturers
Layout:
In this Type 1 prismatic battery pack assembly line, the battery pack busbar is of the bolted type.
Key features:
All types of battery packs for various vehicles, ranging from three-wheelers and cargo to sedan and SUV, are all built on this line.
Highlights:
100% process security, data traceability and operator guidance
Prismatic Battery Assembly Line (Type 2)
Made for a customer making three-wheeler and two-wheeler battery packs
Layout:
In this prismatic battery pack assembly line, the battery pack busbar and side panel will have laser welding.
This line is designed to manufacture 20,000 battery packs per year (in two shifts per day).
Key features:
Automation leader Jendamark supplied a unique cell checking and sorting solution which ensures the right cells being used every time.
Highlights:
Quality gates at every step ensure that each assembly leaving the line is as per product specifications.
Cell-To-Module Line (Segment 1)
Our standard assembly line can be customised as per customer requirements.
Layout:
Individual cells are grouped together to form a module or pack of cells. Jendamark provides the complete solution along with traceability for each cell.
Key features:
Important parameters include open circuit voltage, barcode scanning, bulging, polarity of the terminal and glue dispensing.
Module-To-Pack Line (Segment 2)
We provide the solution along with the traceability of each module.
After the pack assembly, Jendamark seamlessly integrates all the testing machines into its database, so that the customer does not have to look into multiple reports to track product data.
Layout:
This layout is for module-to-pack assembly, where several modules are put together to form a pack.
Key features:
Important parameters include leak testing, glue dispensing, Battery Management System (BMS) testing, all torquing application monitoring and checking.
Cylindrical Cell Line
We designed this line to produce battery packs for two-wheelers.
The entire machine is manufactured in our own factory using collaborative robots (cobots) to eliminate human error and intervention.
We have developed our own machine for cylindrical cell sorting as per OCV/ACIR and AH values.
Layout:
This is a cylindrical battery pack assembly line, in which the battery pack busbar will have resistance spot welding.
The line has the capacity to produce 50,000 battery packs (in two shifts) per year.
Key features:
Important parameters include leak testing, glue dispensing, Battery Management System (BMS) testing, all torquing application monitoring and checking.
Cell-to-Module Line
In this assembly line, Jendamark provides the solution along with traceability of each cell according to key parameters, which can be customised as per customer requirements.
Layout:
Individual cells are grouped together to form a module or pack of cells.
Key features:
Important traceability parameters include Open Circuit Voltage (OCV), barcode scanning, polarity of terminal and glue dispensing.
Module-to-Pack Line
In this assembly line, Jendamark provides the solution along with traceability for each module according to required parameters.
Layout:
Modules are grouped together to form a pack, or bunch of modules.
Key features:
Important required parameters include leak testing, glue dispensing, BMS testing, all torquing application monitoring and checking.
Power Electronics Assembly
The inverter converts electricity from Direct Current (DC) to Alternating Current (AC).
It is one of the most important components of an electric and hybrid vehicle as it provides power for the drivetrain and other high-power-demanding functions of a vehicle.
Explore the various assembly lines we have built by expanding the boxes below:
Inverter Assembly Line
We have provided assembly line solutions for making DC-AC inverters and DC-DC inverters.
Layout:
This inverter assembly line was designed for commercial vehicles and variations are underway for two- and three-wheelers. It features Jendamark’s own integrated Industry 4.0 software solution – ODIN Manufacturing.
Key features:
Auto-tightening with bolt feeder to prevent human error, and auto sealant dispenser for applications like thermal paste, adhesive and meter mixing.
Universal Box Build Line (MCU, VCU, LDC)
We supplied this line for India’s leading electric vehicle manufacturer.
Correct assembly of motor control units, vehicle control units and similar electronic assembly components is critical due to the inherent small size of the child parts.
Key features:
Auto-tightening with bolt feeder to prevent human error, and auto sealant dispenser for applications like thermal paste, adhesive and meter mixing.
Highlights:
This low-volume line has all the process security and data traceability solutions, powered by Jendamark’s own ODIN Manufacturing ecosystem.
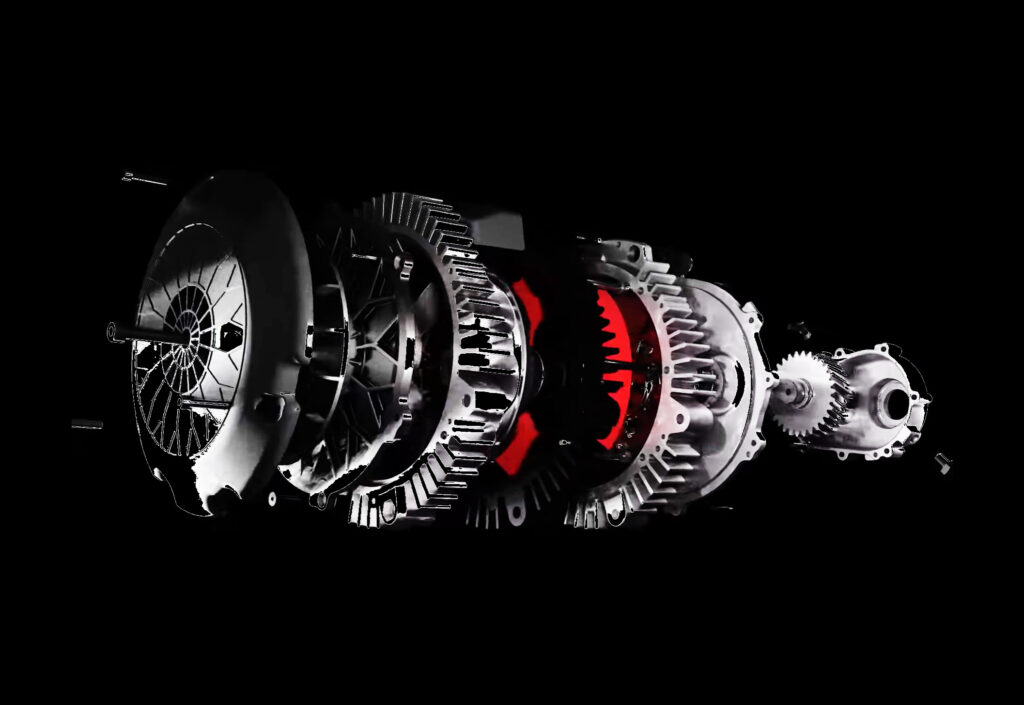
Electric Motor Assembly
Typically, 5 types of motors are used in electric vehicles:
- Brushless DC motor
- Permanent magnet synchronous motor
- AC induction motor
- Interior permanent magnet motor
- Permanent magnet reluctance motor
Explore the various assembly lines we have built by expanding the boxes below:
Motor Assembly Line
We have provided assembly line solutions for EV motors – for every vehicle from two- and three-wheelers to passenger and commercial vehicles.
We provide solutions for complex and challenging assembly requirements such as motor winding, handling the magnets and insertion of the stator into rotor housing.
Layout:
This assembly line solution includes high-precision automatic stator insertion into the rotor. The most challenging part of a motor line is the insertion of stator in rotor housing with strong magnets. This is resolved using a precise gantry system and float arrangement.
Key features:
We also provide high-potential current testing of the motor to check motor winding, as well as a laser marking machine for generating a unique serial number for every part.
Axial Flux Motor Assembly Line
This axial flux motor assembly line is for two-wheeler vehicles. We have provided a solution that features a winding press with 30-ton force.
Layout:
In the assembly line pictured, the machine for dispensing permanent magnets is the most crucial operation – and Jendamark has mastered it.
Key features:
We also provide high-potential current testing of the motor to check motor winding, as well as a laser marking machine for generating a unique serial number for every part.
Rotor Assembly Line
We have manufactured a line for the assembly of rotors – ensuring the right solution at the right time and at the right cost.
Layout:
The complexity of this line involved design, development and manufacturing of stainless-steel fixtures to hold the permanent magnets in position during insertion and baking process.
Key features:
This line has automatic magnet dispensing, auto sealant dispensing, magnet pasting fixture and a baking area for curing sealant.
E-Axle and Gearbox Assembly
Electric vehicles tend to feature fewer moving parts compared to vehicles with internal combustion engines. E-axles, for example, have the entire drive module integrated into their design. While many EVs also don’t require a conventional gearbox due to the near-instant torque, some manufacturers still include multiple gears for better acceleration, efficiency and speed control.
Explore the various assembly lines we have built by expanding the boxes below:
EV Gear Box Assembly Line
We provided an EV gear box assembly line for a reputable Indian brand.
Multiple gears allow an EV to achieve better low-end acceleration and top speed, which help to increase its range. The gears allow the driver to keep the power around a set amount, so they can gradually speed up and slow down while still having sufficient torque.
Key features:
State-of-the-art automatic backlash checking of gear box, cotter pin insertion and other innovative solutions to meet customer product requirements.
Highlights:
Flaring machine, oil seal press machine, automatic sealant dispensing machine, and laser marking machine for generating unique serial numbers for every part.
E-Axle Assembly
E-axles are significantly larger and heavier than traditional axles due to the integration of the electric motor within the axle itself. While traditional axles typically weigh between 120 and 150 kilograms, e-axles can weigh anywhere from 200 kilograms upwards. This substantial increase in weight necessitates adjustments to our assembly processes and equipment.
Key features:
In traditional vehicles, the engine is a separate component, and power is transmitted through a shaft to the differential and then to the wheels. With e-axles, the entire drive module is integrated within the axle, offering improved efficiency and reduced complexity.
Highlights:
Because e-axles incorporate more electrical components, extra precautions to prevent damage from electrostatic discharge (ESD) are required. We have implemented specific measures, such as ESD-safe work surfaces and grounding techniques, to protect these components during handling and assembly.
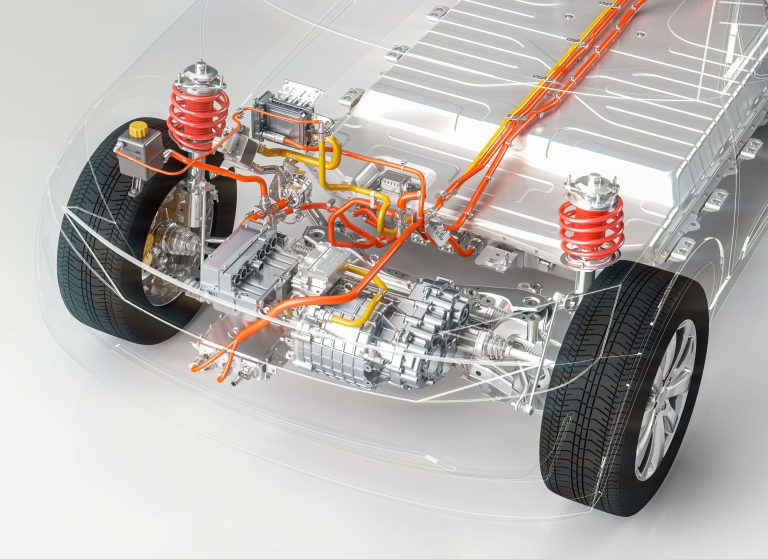
All assembly systems are equipped with our own Industry 4.0 digital solutions, developed to assist with process security, operator guidance, and traceability to ensure quality and consistency of build.
Our modular, building block approach to assembly systems empowers our customers to achieve unmatched flexibility and agility in the dynamic EV market.
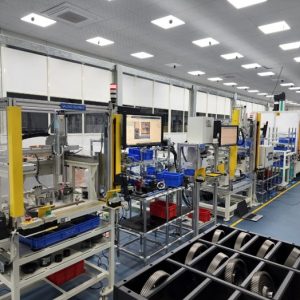
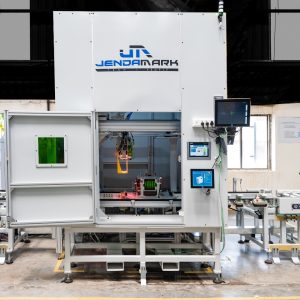
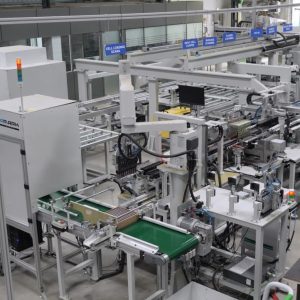
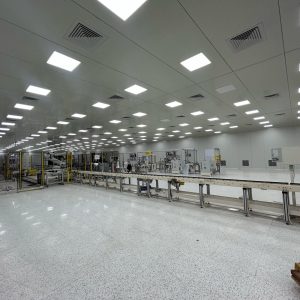
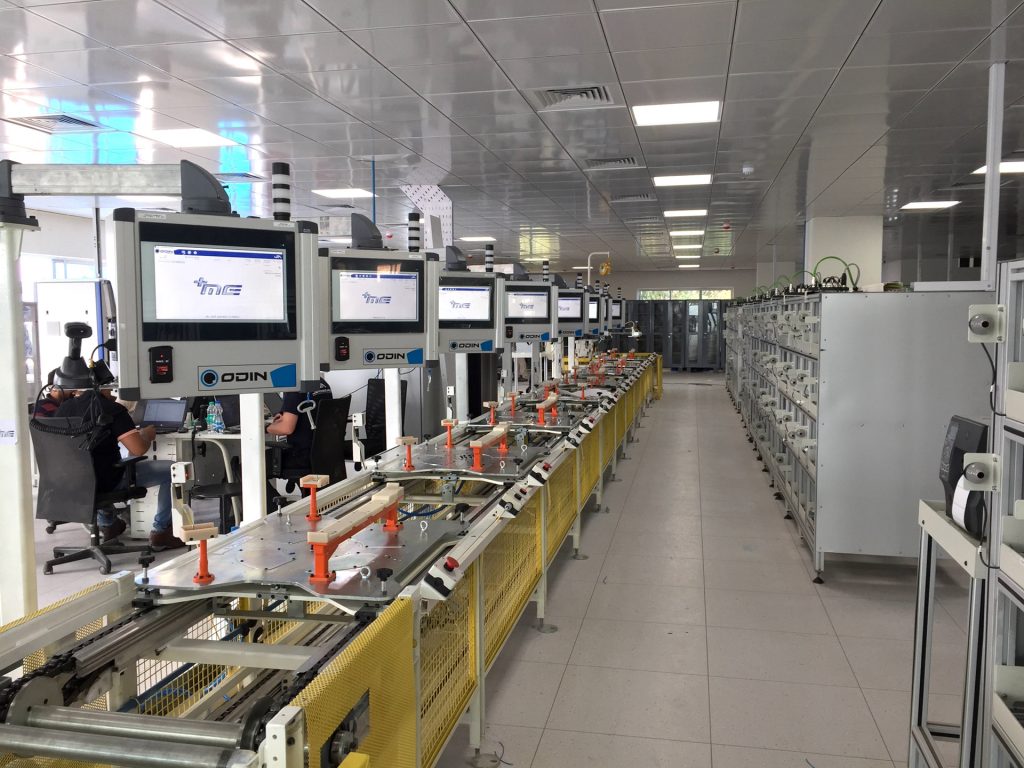
Power up your EV battery pack assembly
Check out our state-of-the-art testing technologies for high-quality, safer EV battery pack assembly.