- Case Study
- Tata
Engine Assembly Line
Building engines better: Smarter manual assembly
How our assembly line operating system ensured 100% data traceability for Tata Motors’ manual engine production
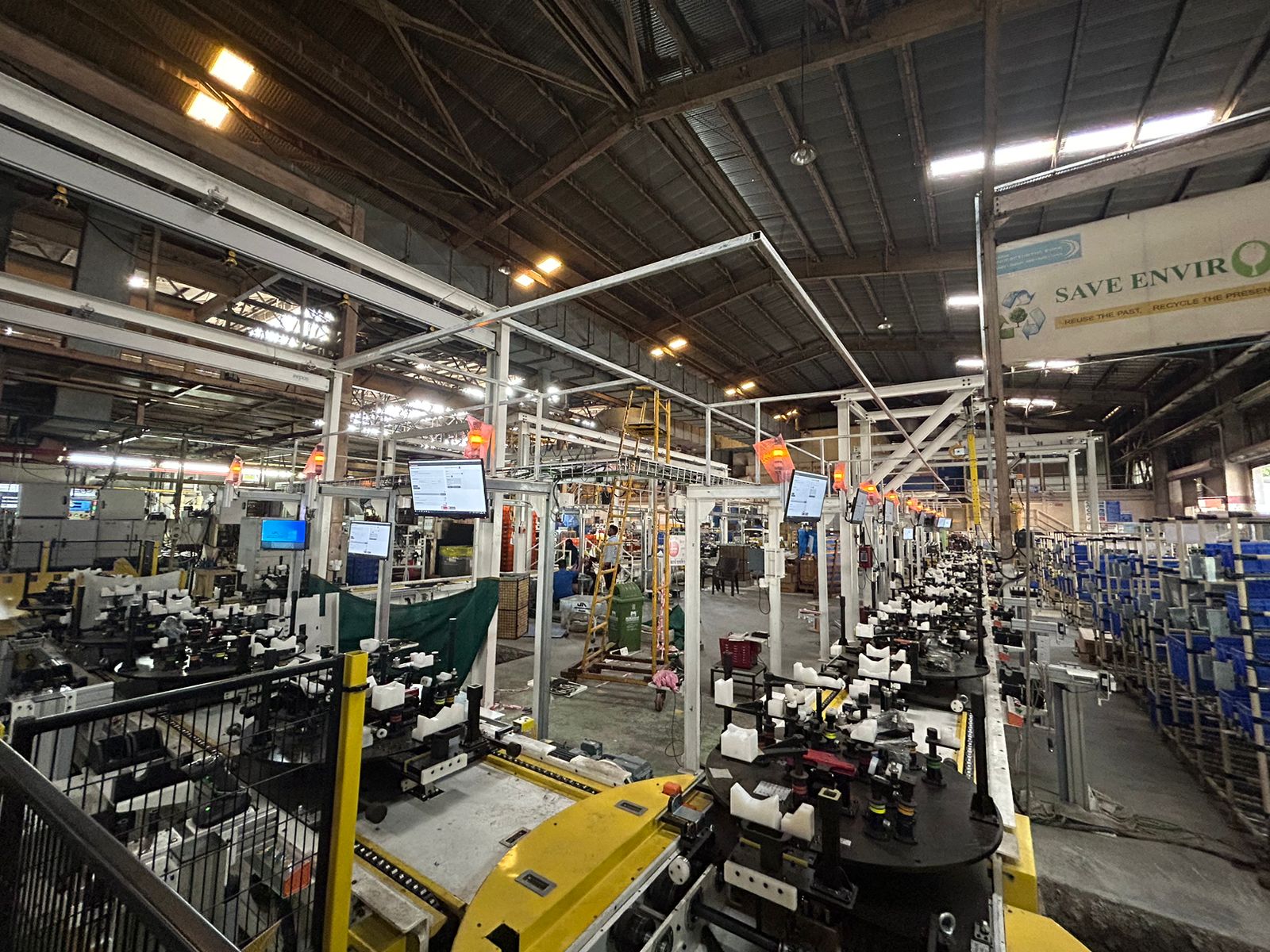
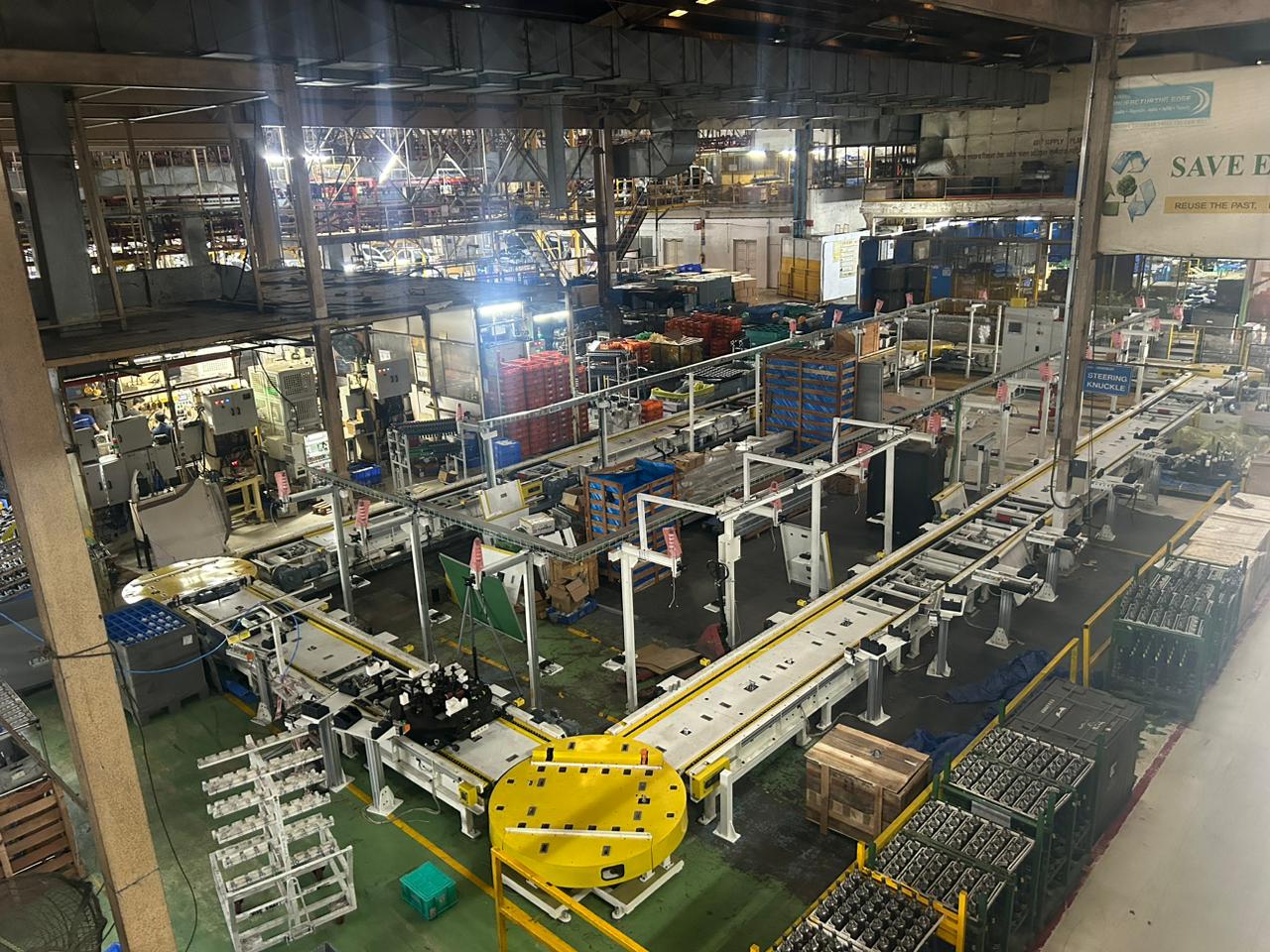
- JENDAMARK DELIVERED
- Pune, India
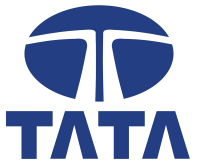
About the Customer
Part of the Tata Group, Tata Motors is a leading global automobile manufacturer of cars, utility vehicles, pickups, trucks and buses. Tata Motors is India’s market leader in commercial vehicles and among the top three in the passenger vehicles market. Tata prioritises human centricity with technological prowess and engineering excellence to make cargo and passenger mobility safer, smarter and greener.
Customer Requirements
Tata Motors wanted to start the digitalisation journey and make assembly at the Pune plant smarter in order to:
- Achieve a quality product
- Ensure complete data traceability for the whole plant
Key Challenges
At its manufacturing facility in Pune, vehicles and engines were still being manually assembled the traditional way.
- Challenge 1 – Process security:
Standard operating procedures were not always followed, especially by operators performing manual operations. Because machine-related mechanical poka-yokes (safeguards) were not in place, some station operations were skipped before passing the part on to subsequent stations, leading to incorrect assembly down the line.
- Challenge 2 – Quality and traceability:
At the quality gate, when a defect was identified, it led to line stoppages and high recovery time, reducing overall equipment effectiveness (OEE) and first time through rates (FTTR).
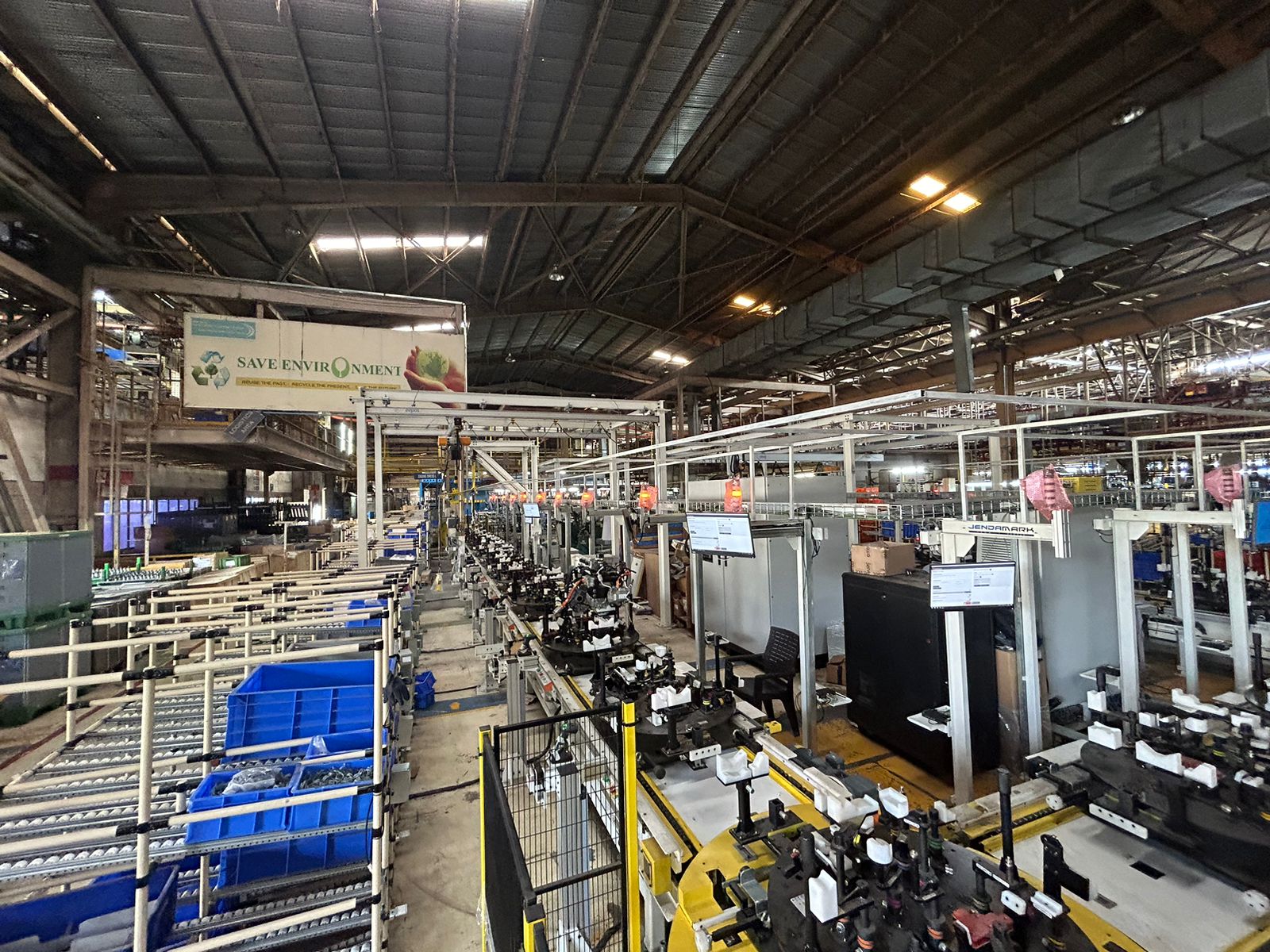
Our Solution
Jendamark implemented ODIN Workstation, our next-level smart manufacturing execution system (MES) or operating system, to make Tata Motors’ engine assembly line smarter.
Solution 1 – Operator guidance:
This digital solution provides step-by-step, visual guidance to ensure that operators follow the correct assembly sequence.
Solution 2 – Process security:
This smart assembly line solution provides all the required mechanical poka-yokes and safety systems. Because it does not allow the part to move on to subsequent stations if steps have been skipped or incorrectly performed, it ensures complete process security and compliance in building a safety critical product.
Solution 3 – Full data traceability:
This is available for every product that comes off the line. If there is a problem, it can be traced rapidly and solved with minimal downtime.
Solution 4 – Real-time reporting:
A real-time analysis of the overall line allows the production management team to see where any problem areas may lie and take corrective action.
Customer Benefits
- Kicked off digitalisation of plant
- Ensured complete data traceability
- Achieved a quality product
Jendamark’s flagship Industry 4.0 solution, ODIN Workstation, has helped Tata Motors in Pune to start their digitalisation journey. As both a worker guidance and process security solution, with deep hardware integration capabilities, it ensures that Tata Motors delivers a well-built, quality end-product with full data traceability for added peace of mind.